Unveiling the Intricacies of Tesla Model 3 Delivery Timeframe
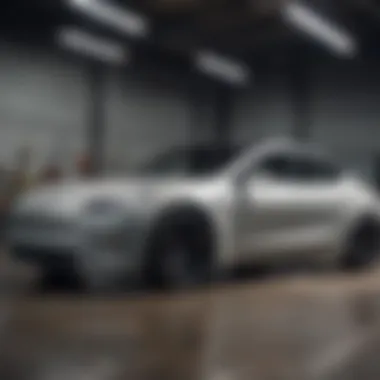
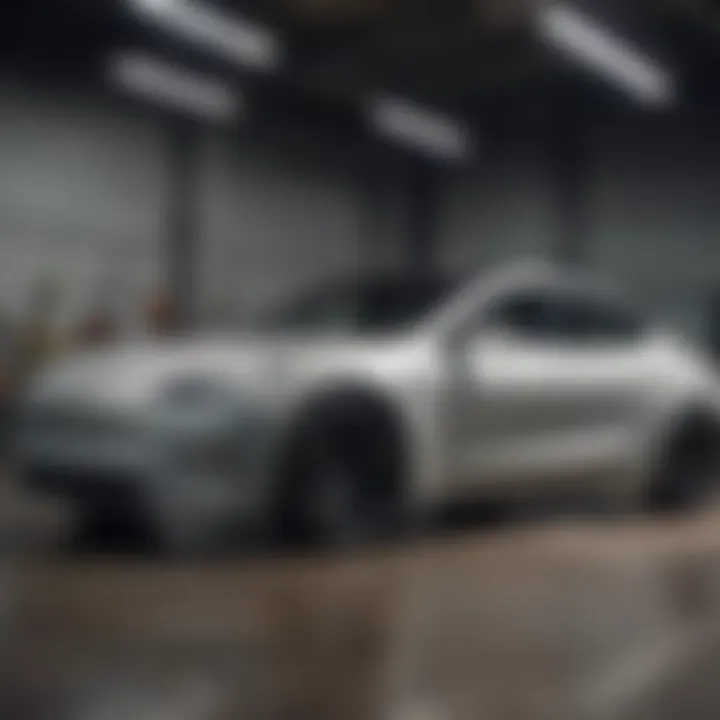
Automotive Latest News
It's a fascinating time for automotive enthusiasts as we delve into the intricate details that encompass the delivery timeline for Tesla Model 3. The realm of automotive news is abuzz with the latest developments surrounding the production, shipment, and delivery of electric vehicles. In recent times, the industry has witnessed a surge in the demand for environmentally conscious cars, driving manufacturers like Tesla to streamline their processes and meet the growing market needs.
New Car Launches
Every new car launch sets the stage for innovation and competition within the automotive landscape. With the Tesla Model 3 making waves in the electric vehicle market, enthusiasts eagerly await updates on production milestones and delivery timelines. The anticipation surrounding new car launches reflects the dynamism of the industry and highlights the evolving preferences of consumers towards sustainable transportation solutions.
Industry Updates
Staying abreast of industry updates is crucial for understanding the shifting dynamics of the automotive sector. From advancements in battery technology to updates in manufacturing processes, each development plays a vital role in shaping the delivery timeline of vehicles like the Tesla Model 3. Industry updates serve as a barometer for assessing the trajectory of electric vehicles in the global market and offer insights into the future of sustainable transportation.
Technological Advancements
The convergence of technology and automotive engineering marks a key turning point in the evolution of electric vehicles. Technological advancements, such as autonomous driving capabilities and enhanced charging infrastructure, are reshaping the delivery experience for customers purchasing the Tesla Model 3. By exploring these technological innovations, enthusiasts can gain a deeper appreciation for the intricate processes that govern the delivery timeline of modern electric vehicles.
Introduction
The underlying foundation of any exploration involving the delivery timelines of products, particularly the highly sought-after Tesla Model 3, is critical in unraveling the complexities of industry operations and consumer expectations colliding. Over the horizons of this article, we embark on a journey delving deep into the systematic orchestration that precipitates the transition of manufacturing brilliance to the hands of eager customers longing for the seamless joy of owning an electric marvel. The essence of understanding the labyrinthine network of processes spanning production, logistics, and finally to the doorstep of the awaiting enthusiast lies within the grasp of our discourse.
In scrutinizing the delivery timelines of the Tesla Model 3, one must not only look at the chronological progression of events but must also immerse themselves in the technicalities that distinguish this modern artifact. The significance of dissecting each facet–compromising stringent production regulations, transportation marvels, and ultimately concluding with the immersive customer experience – becomes apparent as we thread the needle of this deeply woven narrative.
This article serves as a roadmap, guiding enthusiasts and industry professionals alike through the convoluted alleys of manufacturing excellence aligned with consumer satisfaction. The narrative aims not only to inform but to excite the intellect of the astute reader, offering a nuanced view of the meticulous procedures that govern the realm of automotive ingenuity. Embracing this epistemic venture leads us to a comprehensive elucidation of the interconnected elements that culminate in the delivery timelines of the Tesla Model 3, setting the stage for a profound unraveling of this enigmatic journey.
Production Process
In the landscape of automotive manufacturing, the production process holds paramount significance. It serves as the foundation upon which the entire operational framework thrives or falters. The tailored precision in each step, from sourcing components to the final assembly, plays a pivotal role in defining the quality and efficiency of the end product. Understanding the nuances of the production process enlightens stakeholders about the intricate mechanisms at play, ultimately impacting the delivery time of the Tesla Model 3.
Manufacturing
Assembly Line Efficiency
The crux of manufacturing efficiency lies in the optimization of the assembly line. By ensuring seamless coordination of processes, minimizing downtime, and maximizing output, assembly line efficiency stands as a cornerstone of operational excellence. The fluency with which components move along the manufacturing line dictates the pace at which vehicles like the Tesla Model 3 are produced. Any bottleneck in this workflow can ripple across the entire production chain, leading to delays and inefficiencies that directly impinge on delivery timelines. Embracing advanced technologies and lean methodologies, assembly line efficiency streamlines the manufacturing process of the Tesla Model 3, enhancing productivity and precision.
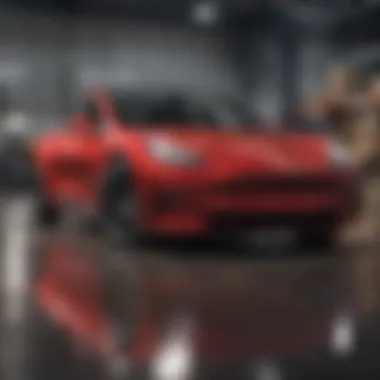
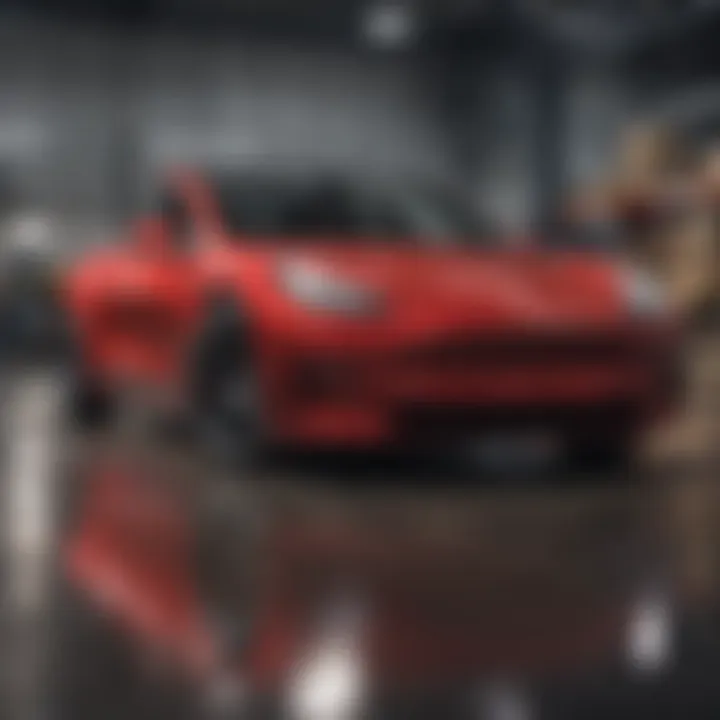
Componenet Sourcing
The sourcing of components represents a critical facet of the manufacturing landscape. A meticulous selection of suppliers, quality checks, and strategic partnerships all converge to ensure a timely and seamless flow of components to the production line. Component sourcing directly influences the overall quality and reliability of the Tesla Model 3. An optimized supply chain not only expedites the manufacturing process but also safeguards against potential disruptions, such as shortages or quality discrepancies. This strategic approach to component sourcing lays the groundwork for a robust production process, fortifying the ecosystem that culminates in the timely delivery of Tesla's flagship electric vehicle.
Quality Control
Testing Procedures
Testing procedures act as the vigilant gatekeepers of production quality. Each test administered during the manufacturing phase serves as a checkpoint, validating the performance, safety, and durability of the Tesla Model 3. Rigorous testing protocols uphold the brand's commitment to excellence, ensuring that every vehicle that rolls off the assembly line meets the stringent quality standards set forth by Tesla. While testing procedures may introduce a layer of complexity to the production timeline, their indispensable role in guaranteeing customer satisfaction and vehicle reliability overshadows any transient delays they may cause.
Standards Compliance
Adhering to industry standards is non-negotiable in the realm of automotive manufacturing. Standards compliance signifies Tesla's unwavering commitment to producing electric vehicles that not only meet but exceed regulatory requisites. By aligning with international quality benchmarks and safety protocols, Tesla bolsters the credibility and market acceptance of the Model 3. While navigating the intricacies of standards compliance may present challenges, the long-term benefits of unfaltering adherence resonate in the form of customer trust, brand loyalty, and operational efficiency.
Logistics and Shipping
Logistics and Shipping play a significant role in the intricate web of processes associated with delivering the Tesla Model 3 to customers. As this article delves deeper into the delivery timeline, understanding the nuances of Logistics and Shipping becomes crucial. It encompasses various elements such as transportation methods, customs clearance, and overseas shipping, all of which are vital to ensure a smooth and timely delivery process. By focusing on the logistics and shipping aspect, this article aims to shed light on how these components influence the overall delivery time for the Tesla Model 3, providing a well-rounded perspective on the journey from production to customer reception. This section will meticulously dissect the crucial role of logistics and shipping in the Tesla Model 3 delivery process, highlighting the intricacies involved and the impact they have on the customer experience.
Transportation Methods
Rail Transport
Rail Transport emerges as a pivotal mode of transporting Tesla Model 3 vehicles, contributing significantly to the efficiency of the delivery process. The key characteristic of Rail Transport lies in its ability to transport multiple vehicles simultaneously over long distances, making it a cost-effective and environmentally friendly choice for shipping. One unique feature of Rail Transport is its reliability in adhering to strict schedules, ensuring timely deliveries to various locations with precision. This section will delve into the advantages of utilizing Rail Transport for shipping Tesla Model 3 cars, shedding light on how this mode of transportation streamlines the delivery process while maintaining high standards of efficiency and reliability.
Overseas Shipping
When it comes to Overseas Shipping, it plays a vital role in expanding the reach of Tesla Model 3 vehicles to international markets, catering to a global customer base. The key characteristic of Overseas Shipping is its ability to facilitate the transportation of vehicles across oceans, enabling seamless connectivity between production facilities and end customers worldwide. One unique feature of Overseas Shipping is its versatility in handling varying shipping distances and customs requirements, making it a preferred choice for reaching distant markets efficiently. By exploring the advantages and disadvantages of Overseas Shipping in the context of delivering Tesla Model 3 cars, this section aims to provide insight into the complexities and considerations involved in ensuring timely and secure international shipments.
Customs Clearance
Import Regulations
Import Regulations encompass a crucial aspect of the delivery process for Tesla Model 3 vehicles, shaping the pathway for seamless customs clearance and international transportation. The key characteristic of Import Regulations revolves around compliance with specific laws and standards governing the import of vehicles into different countries, ensuring legal adherence and smooth transit across borders. One unique feature of Import Regulations is their role in guaranteeing the safety and quality of imported vehicles, safeguarding consumer interests and regulatory standards. By examining the advantages and disadvantages of navigating Import Regulations in the context of Tesla Model 3 deliveries, this section will provide a comprehensive overview of the challenges and benefits associated with adhering to import laws and regulations.
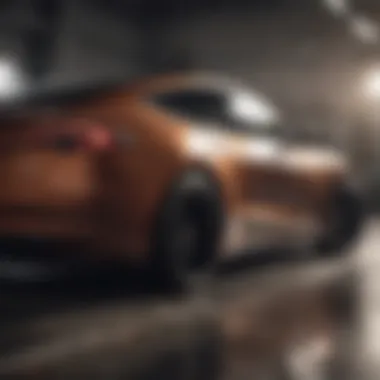
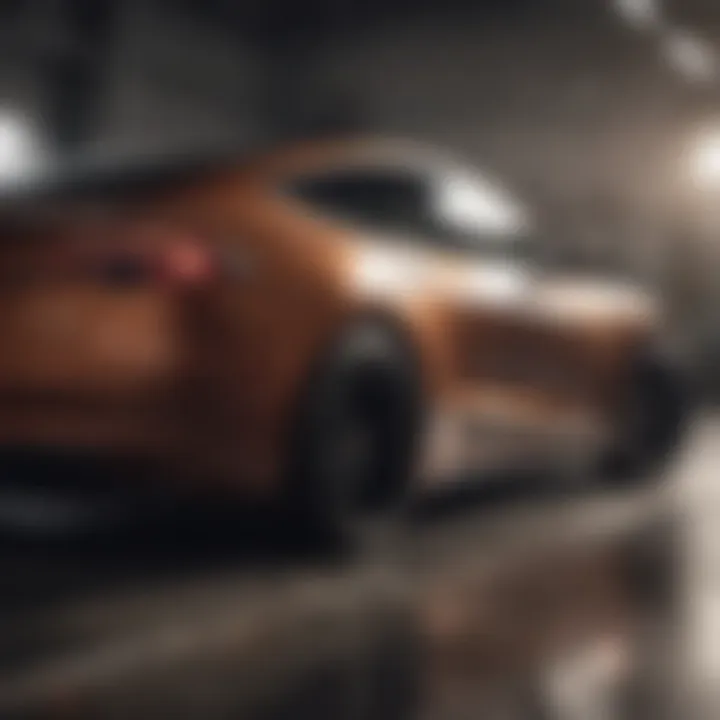
Duties and Taxes
Duties and Taxes form an integral part of the financial considerations involved in shipping Tesla Model 3 vehicles internationally, impacting the overall cost structure and pricing strategy. The key characteristic of Duties and Taxes lies in their role in generating revenue for governments while regulating the flow of imported vehicles into domestic markets. One unique feature of Duties and Taxes is their variability across different regions, influencing the affordability and market competitiveness of Tesla Model 3 cars on a global scale. By analyzing the advantages and disadvantages of handling Duties and Taxes in the context of Tesla Model 3 delivery operations, this section aims to unravel the financial implications and strategic decisions involved in navigating international trade regulations and taxation policies.
Delivery to Customer
The delivery of the Tesla Model 3 to the customer holds significant importance in understanding the entire process chain of this highly sought-after electric vehicle. This final phase signifies the culmination of meticulous planning, manufacturing, logistics, and preparation to ensure a seamless handover of the vehicle to the end-user. Service Centers play a crucial role in this stage, serving as the intermediary between the production facilities and the customers, bridging the gap with efficiency and professionalism. Aiming for utmost customer satisfaction, the delivery process emphasizes the brand's commitment to quality and customer experience.
Service Centers
Appointment Scheduling
Appointment Scheduling within the service centers is a pivotal aspect that streamlines the customer journey towards receiving their Tesla Model 3. This process allows customers to book a specific date and time for their vehicle handover, ensuring a personalized and convenient experience. The key characteristic of Appointment Scheduling lies in its ability to optimize the delivery process, minimizing wait times and providing a tailored approach for each customer. The seamless coordination of appointments enhances customer satisfaction and fosters a positive perception of the brand. Despite occasional challenges such as rescheduling needs, the overall advantages of Appointment Scheduling in expediting the delivery process cannot be overstated.
Vehicle Inspection
Vehicle Inspection represents a critical step in ensuring that every Tesla Model 3 meets the stringent quality standards set by the company. It involves a thorough assessment of the vehicle's components, functions, and aesthetics to guarantee that it aligns with customer expectations. The key characteristic of Vehicle Inspection lies in its role as a quality assurance measure, detecting and rectifying any potential issues before the handover to the customer. This meticulous process enhances overall customer satisfaction by delivering a flawless vehicle while also showcasing Tesla's commitment to excellence. The detailed inspection may introduce minor delays in delivery but underscores the brand's dedication to providing top-tier products and services.
Customer Experience
Handover Process
The Handover Process at Tesla's service centers symbolizes the pinnacle of customer interaction and satisfaction. This phase involves a detailed walkthrough of the vehicle's features, functionalities, and controls, ensuring that the customer is well-versed in operating their new Tesla Model 3. The key characteristic of the Handover Process is its personalized approach, tailoring the introduction to the customer's familiarity with electric vehicles. By offering insights and guidance during this phase, Tesla enhances the overall ownership experience and creates a lasting impression on the customer. While the process may extend the delivery time slightly, the benefits of a well-informed customer far outweigh the temporary delay.
Training and Support
Training and Support mechanisms provided by Tesla post-handover significantly contribute to enriching the customer's ownership experience. This continuous support system offers guidance on maintenance, software updates, and other queries that customers may have after receiving their Tesla Model 3. The key characteristic of Training and Support lies in its proactive nature, anticipating and addressing customer needs before they arise. By enhancing customer knowledge and confidence in utilizing their electric vehicle, Tesla ensures long-term satisfaction and loyalty among its clientele. While additional support may require investment, the advantages of superior customer service in building brand loyalty and advocacy are invaluable.
Factors Affecting Delivery Time
When it comes to the delivery of the Tesla Model 3, numerous factors play a crucial role in determining the timeline from production to reaching the customer's hands. Understanding these factors is essential for both Tesla enthusiasts and potential buyers alike. The delivery time is not just about logistics; it encompasses a holistic view of manufacturing, customization, and geographic considerations. By exploring these elements, individuals can gain a deeper appreciation for the intricacies involved in receiving their Tesla Model 3. Location
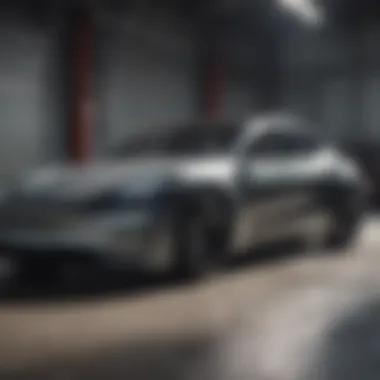
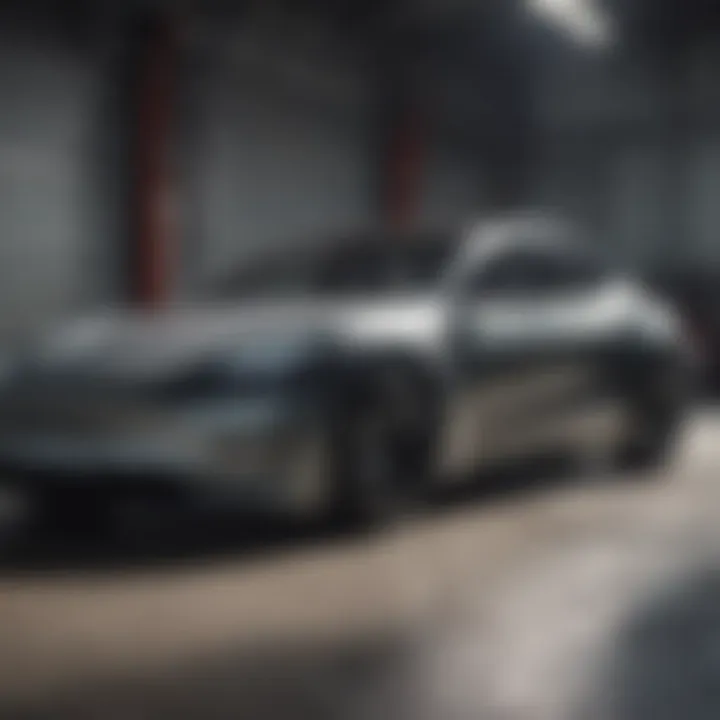
imity to Production Facility
The proximity of a customer to the production facility of Tesla can significantly impact the delivery time. Customers closer to the manufacturing plant typically receive their vehicles quicker compared to those located farther away. The advantage of proximity lies in reduced shipping distances, which minimizes transit time and potential delays in delivery. Having a production facility in close proximity ensures streamlined logistics, making it a preferred choice for customers looking for a swift delivery of their Tesla Model 3. However, one should also consider that proximity might lead to limited customizability options or higher demand in regions close to the facility.
Shi
Distances
Shipping distances, on the other hand, present a different set of considerations for the delivery time of Tesla Model 3. Customers located far from the production facility might experience longer shipping times due to transportation logistics. While Tesla ensures efficient shipment, longer distances inherently introduce the possibility of delays or complications in transit. Understanding the impact of shipping distances is vital for customers to set realistic expectations regarding the timeframe for receiving their vehicle. Despite potential delays, Tesla's robust logistics network aims to minimize transit issues and deliver each vehicle in optimal condition.
Model Con
ation
Custom Featu
he customization of a Tesla Model 3 with specific features can affect the delivery timeline based on production requirements. Opting for custom features introduces a layer of complexity to the manufacturing process, potentially extending the time needed to fulfill an order. While custom features allow for personalization and unique capabilities, they may also lead to longer production times due to the additional steps involved. Customers seeking bespoke elements in their Tesla Model 3 should consider the trade-off between customization and delivery time, ensuring their expectations align with the production implications of their choices.
Production Queue
roduction queue plays a vital role in determining when a customer receives their Tesla Model 3. Tesla's production schedule is carefully planned to accommodate varying degrees of customization and demand for different models. Customers placed higher in the production queue are likely to receive their vehicles sooner than those further down the line. Understanding where one stands in the production queue provides valuable insight into the expected delivery time, allowing customers to anticipate when they can expect to take possession of their Tesla Model 3. Being aware of the dynamics of the production queue helps manage expectations and enhances the overall customer experience.
Customer Expectations
Customer expectations play a crucial role in the entire process of acquiring a Tesla Model 3. When a customer decides to purchase a luxury electric vehicle like the Tesla Model 3, their expectations are naturally heightened. These expectations encompass various aspects, such as the delivery timeline, the condition of the vehicle upon arrival, and the overall customer experience. As a result, Tesla, being a brand known for its innovation and high standards, must ensure that they meet and exceed these expectations to maintain customer satisfaction.
With the growing demand for electric vehicles and sustainable transportation options, customers anticipate timely delivery of their Tesla Model 3. The customers expect transparency throughout the delivery process, from initial order placement to the final handover. They look forward to clear communication regarding any potential delays or updates regarding their vehicle's production and shipment status. Meeting these expectations is crucial for Tesla to uphold its reputation for efficiency and customer service excellence.
Moreover, customer expectations go beyond just receiving the vehicle on time. Customers also have certain quality and performance expectations from their Tesla Model 3. They anticipate receiving a flawless vehicle that aligns with the premium image associated with the brand. Ensuring that each vehicle meets stringent quality standards before delivery is essential to meet and exceed customer expectations. Tesla must also provide adequate support and training to customers upon handover to ensure they fully understand and enjoy the features and capabilities of their new electric vehicle.
Conclusion
In this decisive section, we distill the essence of our exploration into the delivery time for the illustrious Tesla Model 3. The termination of any undertaking holds paramount importance as it amalgamates all antecedent discussions, steering us towards a resolute understanding. The realm of delivery timelines in the automotive industry is a pivotal terrain that dictates customer satisfaction, operational efficiency, and the overarching success of a manufacturer.
Unveiling the complexities shrouding the delivery time for the Tesla Model 3 has unraveled a tapestry of meticulous processes intertwined with uncompromising quality standards. By scrutinizing the multifaceted layers comprising this intricate timeline, we unearth not only the temporal components but also the strategic foresight required in orchestrating flawlessly synchronized operations.
The value of comprehending the variegated influences on delivery time cannot be overstated in this paradigm. From the proximity of the production facility to the intricate dance of customs clearance, each element adds its weight to the chronology of delivering a Tesla Model 3 into the hands of expectant customers. Anticipating and mitigating delays requires a nuanced understanding of these variables, ensuring a streamlined and expedited delivery process.
Moreover, the amalgamation of production efficiency, logistics prowess, and customer centricity crystallizes into the dispatch of a Tesla Model 3 – not just as a car, but as a culmination of technological innovation and consumer anticipation. As we draw the cloak of conclusion around our expedition into the delivery time nuances, we implore stakeholders to delve deeper, to introspect into their own operations, and to glean insights that transcend the specifics of a single model to encapsulate broader principles of excellence.
In summation, the discourse on delivery time for Tesla Model 3 transcends mere temporal considerations. It embodies a narrative of precision, foresight, and seamless execution, setting the stage for a symbiotic relationship between manufacturer and consumer, colored by trust, efficiency, and satisfaction.