Navigating OSHA Regulations in the Automotive Sector
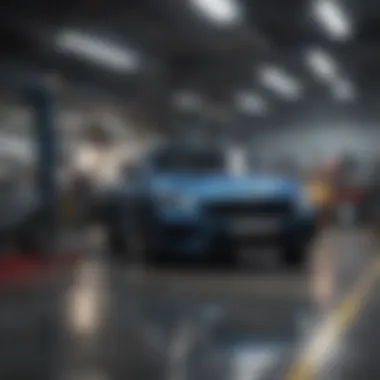
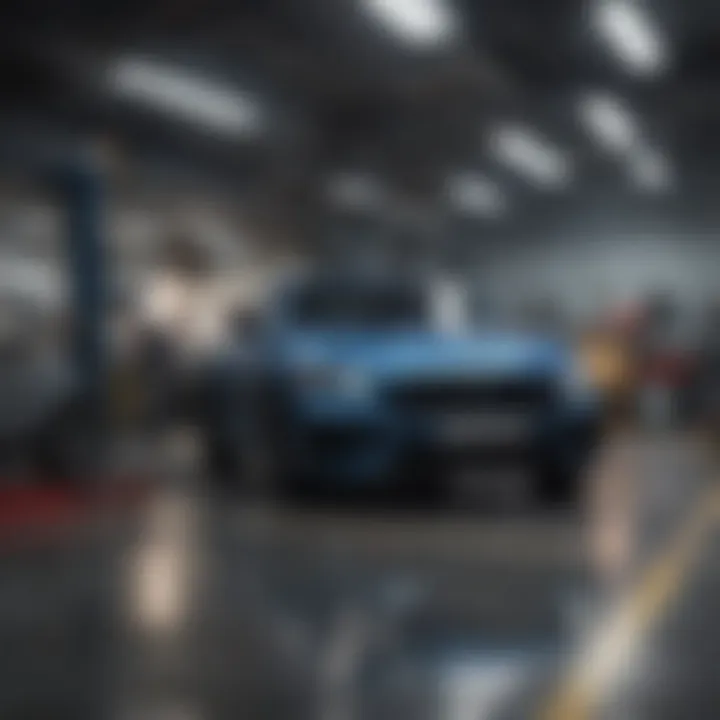
Intro
In the world of the automotive industry, maintaining a safe and compliant workplace goes beyond mere checklists and regulations. It's a landscape shaped by the nuances of OSHA regulations, where every bolt and engine part has an impact on worker safety and environmental health. As the industry evolves, so do the regulations, aiming to foster an atmosphere of safety and efficiency. This article will unpack the intricate relationship between OSHA standards and the automotive sector, providing insights into its history, current regulations, compliance hurdles, and the future of safety protocols.
Through this exploration, we will uncover not just the regulations themselves but the context in which they thrive. Understanding these standards can equip automotive professionals, shop floor workers, and enthusiasts alike with the knowledge necessary to navigate the complexities of safety legislation today. From the origins of OSHA to modern compliance challenges and future trends, these are critical discussions that merit attention in an industry that is both resilient and ever-changing.
Overview of OSHA
Understanding OSHA is pivotal, not only for compliance but for creating a safe working environment within the automotive industry. Regulations set forth by the Occupational Safety and Health Administration (OSHA) mold the foundation of workplace safety. They serve as a blueprint that the automotive sector must follow to prevent accidents, protect workers, and foster an environment of trust and accountability. When one thinks of automotive shops buzzing with activity, it is essential to remember that safety protocols are not just an afterthought; they play a central role in the daily operations of these facilities.
The significance of OSHA cannot be overstated. Enforcing these standards helps mitigate risks associated with the hazards prevalent in automotive work, such as exposure to harmful chemicals, dangerous machinery, and physical strains. Without a robust understanding of OSHA guidelines, a shop can quickly spiral into non-compliance, risking not only the safety of its employees but also facing hefty fines and reputational issues.
Foundational Principles
At its core, OSHA established several foundational principles designed to promote safety and health in the workplace. These principles dictate that every worker has the right to work in environments where hazards are controlled. One of the cornerstones is the "General Duty Clause," which mandates that employers provide a workplace free from recognized hazards.
- Prevention: Prioritize proactive measures to counter risks, rather than merely responding after an incident occurs.
- Communication: Encourage open discussions about safety concerns and practices among team members.
- Engagement: Involve employees in developing safety protocols to promote a culture of awareness.
Furthermore, these principles emphasize training and education, ensuring all workers are equipped with the knowledge necessary for their safety.
Purpose and Objectives
The purpose of OSHA is not solely compliance; it's about instilling a culture of safety. One of the main objectives is to reduce workplace fatalities, injuries, and illnesses through stringent regulations and enforcement. The agency aims to provide regulatory standards that minimize health hazards and ensure a consistent framework for addressing safety issues.
A couple of key objectives include:
- Safety Standards: Establishing comprehensive safety standards that specifically cater to the automotive industry.
- Resource Provision: Offering resources and guidance, so businesses can better understand compliance and safety programs.
- Monitoring Compliance: Ensuring that businesses not only understand but also follow the rules set in place to maintain a safe work environment.
By grasping these core principles, stakeholders can appreciate the broader impact of OSHA on workplace safety and compliance. In a field as dynamic and occasionally hazardous as automotive repair, a firm grasp of OSHA's purpose allows for better preparation and confidence in handling day-to-day operations.
OSHA Regulations Specific to the Automotive Sector
The automotive industry boasts a unique set of risks and challenges, making OSHA regulations both relevant and imperative. The guidelines established by OSHA help organizations navigate these challenges while prioritizing worker safety. Compliance with these regulations contributes to a culture of safety, ultimately benefiting not just employees but also employers by reducing downtime from accidents and fostering a positive workplace environment.
General Industry Standards
General industry standards form the backbone of OSHA regulations, providing a broad framework applicable to various sectors, including automotive. These standards encompass a wide range of topics from workplace safety to health considerations, aligning with the unique requirements of the automotive sector.
Key points in these standards include:
- Hazard communication: Ensuring workers are aware of the chemicals and substances they may encounter.
- Workplace organization: Implementing appropriate signage to highlight risks and maintain clear pathways.
- Emergency preparedness: Outlining procedures to follow in the event of an emergency, such as a fire or spill.
Establishing a clear understanding of these general industry standards is essential for automotive shops. By integrating these regulations into daily operations, automotive professionals can minimize risks, ensuring both compliance and safety.
Hazardous Materials Handling
Handling hazardous materials is a significant aspect of the automotive industry. From oil and lubricants to batteries and cleaning agents, employees encounter various substances that pose risks if not handled properly. OSHA addresses these risks through regulations that mandate safe handling, storage, and disposal practices.
Key considerations include:
- Proper labeling: Ensuring all hazardous materials are clearly labeled to inform employees of potential dangers.
- Training: Regularly educating employees on handling protocols and emergency response measures regarding spills or exposure.
- Personal Protective Equipment (PPE): Specifying the appropriate PPE needed when working with hazardous materials.
Incorporating these practices not only promotes compliance but also enhances the overall safety culture within the workplace. Automotive businesses can protect their employees and reduce liabilities by prioritizing hazardous materials handling.
Machine Safety Requirements
Machinery is at the heart of automotive operations, but it also presents considerable risks. OSHA’s machine safety requirements aim to mitigate these risks, ensuring that equipment is used safely and effectively.
Some essential aspects of machine safety regulations include:
- Guarding: All machinery must have appropriate guards in place to prevent accidents.
- Lockout/Tagout procedures: When performing maintenance, ensuring machine energy sources are properly shut off to prevent unintended start-ups.
- Regular inspections: Implementing a routine to inspect machinery for wear and tear to maintain operational safety.
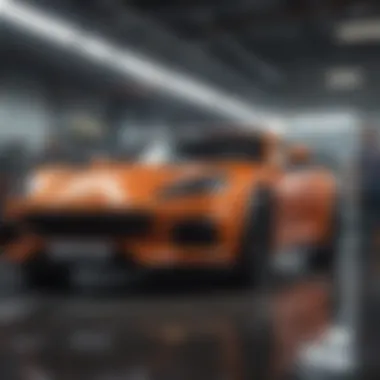
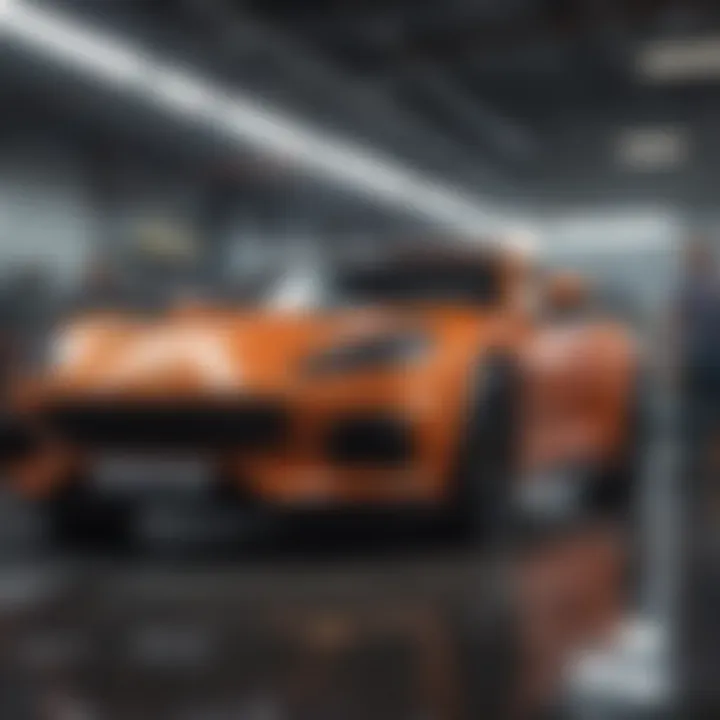
Ensuring compliance with machine safety requirements not only protects employees but also cultivates efficiency in operations. A workplace that prioritizes machinery safety ultimately experiences fewer accidents and enhances productivity.
"An organization that knows how to safeguard its workers ensures a foundation of success and stability wherever its wheels may roll."
In summary, OSHA regulations serve as a critical framework for automotive industry professionals. Understanding and integrating general industry standards, proper hazardous materials handling, and stringent machine safety requirements are fundamental in promoting a safe and productive automotive environment.
Key Safety Practices in Automotive Workshops
In the automotive industry, safety is not just a protocol; it's the foundation on which operational efficiency rests. Key safety practices serve as essential guidelines that protect workers from harm, ensuring a safer workplace. Employers and employees alike share the responsibility of fostering an environment where safety takes precedence over speed and convenience. Understanding these key practices can lead to significant benefits, including reduced incidents, enhanced morale, and overall operational reliability.
Personal Protective Equipment (PPE)
Personal Protective Equipment is the frontline defense against on-the-job hazards in automotive workshops. The variety of risks—ranging from chemical exposure to physical injuries—makes the use of PPE crucial.
From safety goggles to reinforced gloves, the right equipment can*** make a world of difference***. For instance, using appropriate eyewear protects the eyes from flying debris when grinding metal. Similarly, durable gloves not only prevent cuts but also shield against harmful substances:
- Safety goggles: Protect against dust, chemicals, and projectiles.
- Shoe protection: Steel-toed boots minimize risks from heavy falling objects.
- Hearing protection: Earplugs or earmuffs safeguard against excessive noise levels.
Fostering a culture that prioritizes PPE helps ensure that every employee remains keenly aware of the hazards they face. Regular training sessions and clear maintenance schedules for this equipment ensure it is always in top-notch condition.
Ergonomics in the Workplace
Ergonomics is crucial in preventing workplace injuries, especially in environments where manual labor predominates. In the automotive industry, repetitive motion injuries are all too common. By designing tasks and workplaces that adapt to human physical capabilities, employers can significantly reduce strain and fatigue, which often lead to injuries.
Adopting ergonomic practices includes:
- Adjustable workstations: Allow workers to modify their environment to suit their needs.
- Proper lifting techniques: Teach employees how to lift heavy items safely, ensuring they bend at the knees, not the back.
- Taking breaks: Regular pauses help alleviate discomfort, keeping workers refreshed.
Ergonomics is not just about comfort; it directly influences worker productivity and satisfaction. A workforce that feels cared for in terms of their physical well-being is often happier and more efficient, translating to better overall performance.
Emergency Preparedness
Every workshop should have a robust emergency preparedness plan. A well-thought-out approach helps in swiftly addressing potential emergencies, from chemical spills to fire outbreaks. When sudden situations arise, having a plan can mean the difference between chaos and a well-coordinated response.
Key components of emergency preparedness include:
- Regular drills: Routine practice prepares staff for different emergency scenarios.
- Clear signage: Easily visible exit routes and safety equipment locations prevent confusion in high-stress moments.
- Communication systems: A reliable means to alert and inform all workers during emergencies aids quick evacuation and response.
"Preparedness is the first step towards safety; it’s the bridge between awareness and action."
Training and Education
The automotive industry thrives on innovation, efficiency, and most importantly, safety. A cornerstone of maintaining safety in workplaces, especially those dealing with automotive repair and manufacturing, is robust training and education programs. These programs go beyond just ticking boxes; they play a pivotal role in shaping a safety-oriented culture and ensuring compliance with OSHA regulations.
Effective Safety Training Programs
To drive home the importance of safety, a company’s training program should be tailored specifically to the challenges of the automotive field. This begins with a deep understanding of the daily risks faced by employees. Safety training must not be a one-time event but rather an ongoing dialogue that empowers staff.
Here are several elements that an effective safety training program should include:
- Hands-on Training: Simulated situations allow employees to practice their responses to various hazards.
- Regular Refreshers: New regulations or improved techniques should be communicated regularly to keep safety measures fresh in the minds of workers.
- Interactive Learning: Incorporating quizzes or discussion sessions can enhance retention.
- Mentorship Opportunities: Pairing new employees with seasoned workers fosters a culture of safety and experience sharing.
Certification and Compliance
Compliance with OSHA can feel like navigating a maze, but a well-structured approach to certification simplifies the process. Successful certification entails documenting training efforts alongside understanding current regulations. This helps create transparency and build a culture of accountability.
Benefits of focusing on certification include:
- Credibility: A certified workforce is often seen as more capable and professional, boosting the company’s reputation.
- Reduced Liability: Should an incident occur, having a strong foundation in training means you're less exposed to lawsuits or financial penalties.
- Improved Morale: When employees know they are well-trained and compliant, it affects their confidence and overall job satisfaction positively.
"Training isn’t just a compliance issue; it’s a moral obligation. We owe it to our employees to keep them safe on the job."
Lastly, staying connected with OSHA updates is pivotal in a fast-paced environment like automotive. Engaging with resources such as the Occupational Safety and Health Administration can keep organizations well-informed about regulatory changes.
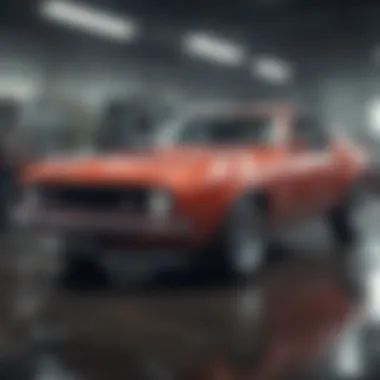
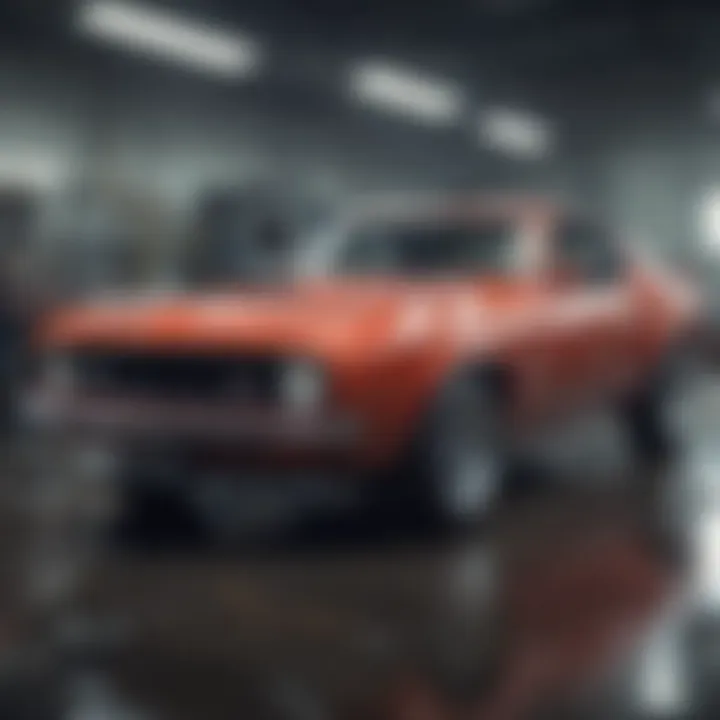
Compliance Monitoring and Reporting
Compliance monitoring and reporting play an essential role in ensuring that automotive businesses adhere to OSHA regulations. Properly executed monitoring helps create a safer workplace, protecting employees from hazards that could lead to injury or illness. After all, a well-maintained safety culture not only reflects a company's commitment to its workforce but also safeguards its reputation in the industry.
One of the significant benefits of compliance monitoring is the proactive identification of potential issues before they escalate into serious incidents. Regular inspections and audits allow businesses to catch compliance lapses or dangerous conditions while there's still time to address them. This might include checking safety equipment, evaluating workspace ergonomics, or ensuring that Material Safety Data Sheets (MSDS) are up-to-date and accessible.
It's also crucial to have a clear understanding of the specific elements involved in compliance monitoring:
- Establishing a Regular Schedule for Inspections: Creating a timeline for reviews and audits ensures that compliance tasks are not overlooked. Frequent evaluations help maintain a continuous awareness of safety standards.
- Documentation and Reporting: Accurate records of inspections and audits form the backbone of compliance reporting. It’s vital to document findings and corrective actions taken to address any deficiencies uncovered during evaluations.
- Employee Involvement: Engaging employees in compliance monitoring often yields substantial benefits. Workers are typically the first to notice unsafe conditions. Thus, fostering a culture where employees are encouraged to report hazards can lead to a safer environment.
- Collaboration with Regulatory Authorities: Maintaining an open line of communication with OSHA and other regulatory bodies can provide invaluable insights into compliance expectations and upcoming regulatory changes.
Implementing effective compliance monitoring and reporting can have advantageous ripples throughout an organization. By placing an emphasis on safety, companies may notice a decrease in accidents and injuries leading to reduced downtime and financial burdens.
"The key is not just to comply, but to cultivate a culture where safety is an integral part of daily operations."
Overall, the ongoing evaluation and adaptation of compliance strategies help organizations stay ahead of regulatory requirements, ultimately paving the way for a safer automotive workplace.
Inspections and Audit Processes
Inspections and auditing processes are vital to ensuring that facilities adhere to OSHA regulations. These procedures are systematic methods of examining safety measures and evaluating compliance against industry standards.
During inspections, safety officers will look for adherence to regulations related to:
- Use of PPE: Appropriate personal protective equipment needs to be used at all times, and audits should confirm that it is correctly utilized and maintained.
- Use of Machinery: Evaluating equipment for safety certificates and ensuring that guards and safety features are in working order.
- Chemicals and Hazardous Substances: Checking that proper storage, labeling, and disposal measures are in place.
Audits can be internal, where the company conducts its review, or external, where regulatory bodies assess compliance. Each type of audit has its value and revelation, giving a fresh perspective to safety practices.
Incident Reporting Procedures
Incident reporting procedures form a pivotal aspect of maintaining workplace safety. When an incident occurs, whether it's a near miss or an actual accident, the response must be swift and effective.
Here’s a breakdown of critical elements in incident reporting:
- Immediate Response: In case of an accident, it's paramount to ensure safety first. Employees should be trained on first aid and emergency protocols.
- Documentation: Every incident should be meticulously documented. This includes when and where it happened, individuals involved, and the nature of the incident. The more detailed the report, the better equipped the company will be to prevent future occurrences.
- Root Cause Analysis: After an incident, understanding the underlying reason is crucial. Are there environmental factors, underlying procedural flaws, or gaps in training that need to be addressed?
- Reporting to OSHA: Depending on the severity of the incident, it may be mandatory to report it to OSHA within a specific timeframe. This is an essential step in ensuring compliance with legal requirements and can demonstrate a company’s commitment to accountability and transparency.
By carefully monitoring and reporting compliance, companies in the automotive industry can foster an environment where safety is paramount, thus enabling them to navigate the complexities of OSHA regulations more effectively.
Impact of Non-compliance
Understanding the impact of non-compliance with OSHA regulations in the automotive industry is not just an academic exercise; it’s a matter of life, safety, and business efficacy. Failing to comply with these regulations can lead to severe consequences, affecting not only the workforce but also the business's bottom line and public image. The investigation into these repercussions provides valuable insights into maintaining workplace integrity and operational success.
Legal Implications
Non-compliance opens a Pandora’s box of legal implications. For one, businesses found lacking in their adherence to OSHA standards could face hefty fines. These penalties can range from thousands to millions of dollars, depending on the severity of the violations. Moreover, persistent disregard for safety standards could result in more serious legal actions—such as lawsuits from injured employees or even criminal charges against responsible parties.
Some notable legal implications include:
- Increased Scrutiny: A history of violations can result in increased inspections by OSHA, putting added strain on the operations.
- Loss of License: In extreme cases, businesses may find their operating licenses suspended or revoked, effectively shutting them down.
- Insurance Issues: Liabilities rise when there’s a non-compliance status, often leading to increased premiums or loss of coverage.
The specter of legal troubles looms large; it’s crucial for automotive businesses to not only align with OSHA regulations but to proactively exceed them whenever possible. This not only mitigates risks but also fosters a culture of safety and accountability.
Reputation Damage
The damage to a company’s reputation can be as detrimental as its legal woes. Non-compliance often leads to negative media coverage, which can tarnish a company’s image in a market where trust and transparency matter greatly. Automotive enthusiasts and professionals alike are becoming increasingly aware of workplace safety and corporate responsibility. Therefore, when a brand does not uphold these standards, the public's perception shifts unfavorably.
Consider the following impacts on reputation:
- Loss of Customer Trust: Customers are more likely to shy away from brands known for unsafe practices. An automotive company caught in violation may find loyal customers looking elsewhere at the first sign of trouble.
- Employee Morale: If employees feel unsafe or undervalued, morale plummets. A workforce that lacks confidence in the company’s commitment to safety can lead to increased turnover and difficulty attracting top talent.
- Market Position: In industries like automotive, where competition is fierce, reputation is everything. A company with a blemished safety record can quickly fall behind industry competitors who prioritize compliance and safety.
"In the realm of business, reputation is often built on the foundation of safety and trust. One misstep can unravel years of investment in public perception."
Future Trends in OSHA Regulations for the Automotive Industry
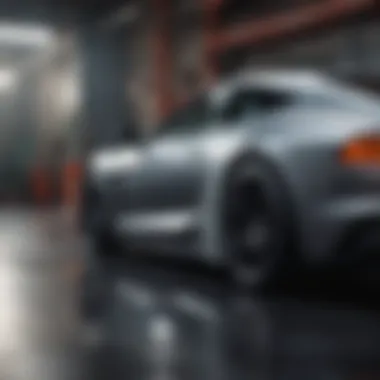
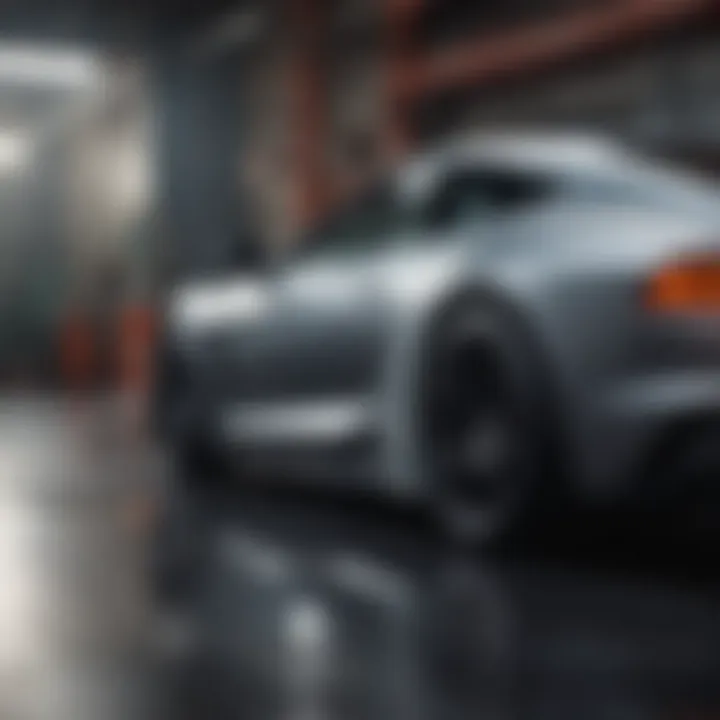
The landscape of occupational safety and health is continually evolving, particularly within the vibrant world of the automotive industry. Understanding the future trends surrounding OSHA regulations is crucial for those invested in this sector, whether they're seasoned professionals or passionate enthusiasts. As technology advances and societal expectations shift, so too do the regulations aimed at keeping workers safe.
There’s no denying that adapting to the changing times can be a difficult task, but recognizing and embracing these shifts can lead to several benefits. Enhanced compliance not only boosts safety on the ground but also helps organizations mitigate risks associated with accidents and legal repercussions. Moreover, effective incorporation of future trends into policy can foster a culture of safety that permeates all levels of an organization.
Technological Advancements and Safety
Technology is increasingly becoming a cornerstone in the automotive industry. From automation and advanced imaging systems to state-of-the-art diagnostics, the journey ahead is filled with innovations that promise safety and efficiency. Not only do technological advancements facilitate the creation of safer working environments, but they also enable organizations to uphold stringent compliance with OSHA regulations.
Consider the role of Artificial Intelligence and Machine Learning in predictive maintenance. These technologies can analyze vast amounts of data to anticipate potential equipment failures before they pose risks to workers. As a result, incidents can be minimized, and hazardous conditions neutralized proactively. Furthermore, enhanced wearables, like smart helmets embedded with sensors, can monitor environmental conditions and alert employees to potential hazards, ensuring a quicker response to safety concerns.
In the realm of training, virtual reality is making waves as an effective tool for providing immersive safety training. Employees can engage in realistic simulations without putting themselves in harm's way. The benefits of such programs include reduced incidence of injuries during actual work and heightened retention of crucial safety practices. The integration of these technologies into training and operations reflects a forward-thinking approach that is essential in the modern automotive workplace.
Evolving Regulatory Landscape
Regulations are not static; they transform to reflect new knowledge, technologies, and social expectations. In the automotive realm, this evolution is particularly pronounced, with OSHA periodically reassessing standards to address to current and emerging risks. The focus is increasingly on preventive measures rather than reactive responses, placing an emphasis on holistic safety practices throughout the organization.
One significant aspect of this evolving landscape is the drive towards sustainability and environmental safety. As the world grapples with climate change, OSHA is likely to incorporate more regulations that address not just worker safety but also the environmental impact of automotive operations. This includes proper handling of hazardous materials, like oils and chemicals, and the sustainability of manufacturing practices.
Moreover, there’s a growing recognition of mental health as part of the comprehensive safety paradigm. Upcoming regulations may reflect an integrated approach that caters to both physical and psychological well-being at work. Organizations that preemptively adjust their policies to encompass these shifts will likely see improved morale and productivity.
“In order for the automotive industry to thrive, it must stay ahead of the curve in adopting regulations that foster both safety and innovation.”
The unique intersection of technological advancements and evolving regulations presents a roadmap for future compliance approaches in the automotive sector. Organizations that actively engage with these trends stand to benefit not just legally but also in their overarching commitment to creating a safer workplace for all involved.
Case Studies and Real-World Applications
In the sphere of OSHA regulations and the automotive industry, case studies may serve as a powerful tool. They provide not just theoretical knowledge, but practical insights that can deeply resonate with automotive professionals and enthusiasts alike. These real-world applications highlight both the successful strategies implemented by companies and the pitfalls encountered due to non-compliance. Analyzing these cases makes it easier to translate regulatory standards into everyday practices, emphasizing the relevance of safety measures at every turn.
By delving into case studies, one can identify trends that reflect the practical adherence to regulatory standards. They offer a lens to view how different organizations deal with hazards and what effective strategies look like in real life. Rather than learning from abstract examples often found in textbooks, industry stakeholders can benefit from observing how their peers have navigated similar challenges.
There are several benefits to focusing on case studies in the automotive sector:
- Illustration of Success: Companies that successfully implemented OSHA regulations often report reduced workplace injuries and improved worker morale. This serves as a vital reminder that prioritizing safety is not just about compliance but also about fostering a healthy work environment.
- Opportunity for Improvement: Analyzing unsuccessful cases can reveal common missteps and compliance failures. This insight is critical for organizations to refine their paths and bolster their safety practices.
- Empowerment Through Knowledge: Knowledge sharing fosters a culture of awareness, encouraging organizations to take proactive approaches rather than reactive ones when it comes to safety. By studying what others have done, entities within the automotive industry can learn from previous mistakes and triumphs.
"The best way to predict the future is to create it."
- Peter Drucker
Through this perspective, case studies can contribute to a collective responsibility toward maintaining higher safety standards throughout the automotive industry.
Successful Compliance Strategies
A notable case is that of a medium-sized auto repair shop that struggled with hazardous material storage. This shop had multiple compliance issues concerning the proper storage of flammable liquids. By consulting with an OSHA expert and engaging in a comprehensive review of their practices, they developed strategies that significantly improved their compliance status.
- Regular Safety Audits: Conducting semi-annual safety audits became a priority. This not only ensured adherence to OSHA standards but also identified potential hazards before they could lead to serious incidents.
- Employee Training: The shop implemented regular training sessions for all employees on proper hazardous materials handling and emergency procedures. They utilized real scenarios to enhance the learning experience.
- Visual Cues: Color-coded signage was introduced to indicate areas where specific hazards were present. This simple change heightened overall awareness and contributed significantly to maintaining a safer work environment.
These successful strategies not only ensured compliance but also fostered a culture focused on safety.
Lessons Learned from Violations
Another stark illustration arises from a large automotive manufacturing facility that faced significant penalties due to a fatal accident involving machinery. The investigation revealed that the company had neglected the requisite safety measures for machine operation, including proper lockout/tagout procedures.
Key takeaways from this violation included:
- Communication Failures: Clear channels of communication regarding safety protocols were inadequate. Employees reported they had not been trained effectively on machine safety.
- Lack of Maintenance: The facility’s machinery had not undergone necessary maintenance checks, leading to unsafe operating conditions.
- Compliance Culture: There was a pervasive attitude that compliance was a mere checkbox exercise rather than integral to the company’s operational philosophy.
The repercussions of this violation rippled through the organization—financially, morally, and operationally. It underscored the need for a robust compliance framework that goes beyond mere adherence; it requires a paradigm shift where safety becomes a shared responsibility among all employees.
Closure
The importance of the conclusion in this article lies in its ability to encapsulate the essential themes discussed throughout the various sections. It serves as a crucial synthesis of the intricate relationship between OSHA regulations and the automotive industry, which facilitates worker safety, environmental responsibility, and operational efficiency.
Summarizing Key Points: The article highlighted vital aspects such as compliance monitoring, specific OSHA regulations tailored for the automotive sector, and the implications of non-compliance. Each section has equipped readers with an insight into how regulations play a pivotal role in shaping safe working environments. The discussion on training and education reinforced that knowledge and methodical practices are cornerstones of maintaining safety standards.
Moreover, the case studies showcased real-world applications, providing tangible evidence of how adherence to such regulations not only protects workers but also enhances the overall reputation of automotive organizations. Perspectives on future trends, including technological advancements, forecast a shift towards even stricter compliance measures, ensuring safety remains at the forefront of industry priorities.
The Way Forward: Moving forward, the automotive industry must embrace a proactive stance in adapting to changing regulations. Making safety protocols second nature should be the goal. Continuous education and training programs will help reinforce a culture where compliance is not merely a checkbox exercise but ingrained within the company's ethos.
Leadership within automotive businesses ought to champion these practices, emphasizing the tangible benefits of a robust workplace safety approach, which includes not only avoiding legal pitfalls but also fostering trust among employees and enhancing customer satisfaction.