Mastering HP Multi Jet Fusion Design to Achieve Unrivaled Results
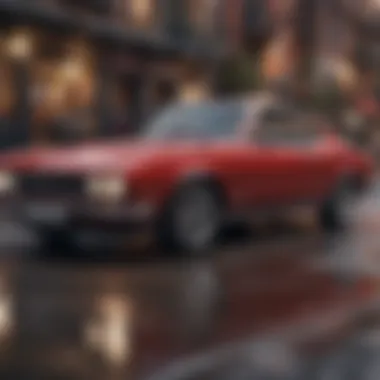
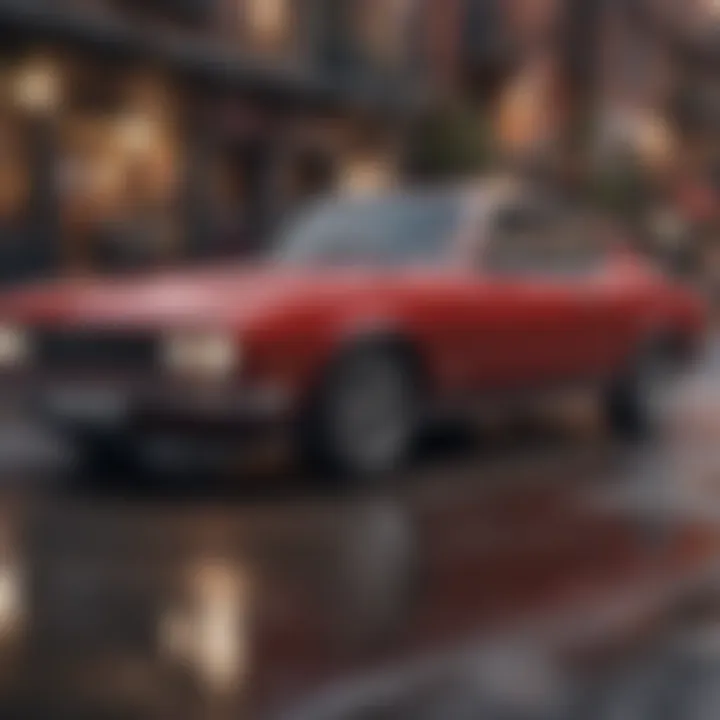
Automotive Latest News
As we delve into optimizing HP MJF design for superior results, staying abreast of Automotive Latest News becomes crucial. It's essential to be aware of the latest developments in additive manufacturing within the automotive industry, especially in the realm of design optimization.
Car Reviews
Examining Car Reviews provides valuable insights into how HP MJF technology is shaping the perception of vehicles in terms of design and performance. Expert Reviews shed light on the intricate details of additive manufacturing applications, while User Ratings offer real-world feedback on the usability and aesthetic appeal of MJF-produced automotive parts. Comparing these components with traditional manufacturing methods can reveal the true potential of HP MJF design optimization.
How-To Guides
Navigating How-To Guides offers practical tips and step-by-step instructions for optimizing HP MJF design. Whether it's understanding Maintenance Tips to prolong the lifespan of 3D-printed automotive components or exploring DIY Repair Guides for quick fixes, these resources empower enthusiasts to harness the full potential of MJF technology. Additionally, Performance Upgrades showcase the endless possibilities of HP MJF design optimization in enhancing vehicle functionality and aesthetics.
Automotive Events Coverage
Exploring Automotive Events Coverage unveils the intersection of HP MJF technology and the automotive world. From Auto Shows showcasing cutting-edge designs to Car Races highlighting the performance capabilities of additive manufacturing, these events provide a platform to witness firsthand the impact of HP MJF design optimization. Industry Conferences further delve into the future trends and innovations driving additive manufacturing in the automotive sector.
Featured Articles
Within Featured Articles, a spotlight is cast on the intricacies of optimizing HP MJF design. Delving behind-the-scenes at Car Manufacturers unveils the intricate processes involved in leveraging MJF technology for automotive applications. An exploration of Future Trends and Innovations showcases the evolving landscape of additive manufacturing, offering a glimpse into the possibilities that HP MJF design optimization holds for the future of the automotive industry.
Introduction to HP MJF Technology
In delving deep into the realm of HP Multi Jet Fusion (MJF) technology, one must first grasp the fundamental pillars upon which this innovative printing methodology stands. HP MJF has firmly established itself as a frontrunner in the realm of additive manufacturing, pioneering a path towards unparalleled precision and efficiency. The essence of HP MJF lies in its ability to fuse intricacy with swiftness, creating intricate designs with remarkable speed, a feat that had previously eluded traditional manufacturing methods. The allure of HP MJF technology gravitates towards its capacity to revolutionize design processes, offering a myriad of possibilities for creating intricately detailed components that cater to a spectrum of industries, with automotive engineering standing at the forefront of its beneficiaries.
The ramifications of embracing HP MJF technology cascade across various sectors, with automotive engineering standing as a prominent benefactor. The infusion of HP MJF into the automotive design sphere heralds a new era of possibilities, marked by enhanced structural integrity, heightened design flexibility, and accelerated production timelines. By leveraging the capabilities of HP MJF, automotive enthusiasts can transcend the constraints of traditional manufacturing, venturing into a realm where intricacy meets functionality seamlessly. The crux of HP MJF's significance in automotive design lies in its ability to democratize access to intricate part production, dismantling conventional barriers and ushering in a new epoch characterized by unparalleled design freedom and manufacturing efficiency.
Key considerations surrounding HP MJF plot a roadmap towards meticulous design optimization. In navigating the terrain of HP MJF design guidelines, one must embrace a paradigm shift towards precision and foresight. Understanding the nuances of wall thickness optimization, support structure considerations, and strategic part orientation becomes imperative in harnessing the full potential of HP MJF technology. By articulating these intricate design guidelines, automotive professionals can transcend mediocrity and embrace a realm where superior results and operational efficiency converge seamlessly, redefining the contours of contemporary automotive design and production processes.
Understanding Design Guidelines for HP MJF
Understanding Design Guidelines for HP MJF is paramount in comprehensively grasping the nuances of optimizing designs for HP Multi Jet Fusion (MJF) technology. By focusing on Designing for Accuracy and Consistency, Enhancing Mechanical Properties, and Ensuring Printability and Build Success, this section delves into the depths of designing components that meet the highest standards of excellence.
Designing for Accuracy and Consistency
Optimizing Wall Thickness
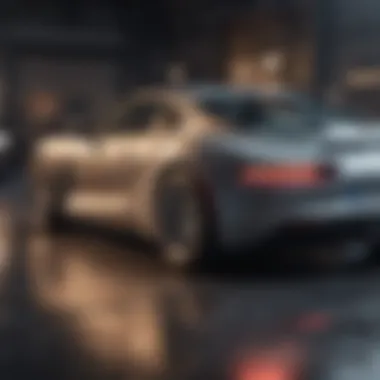
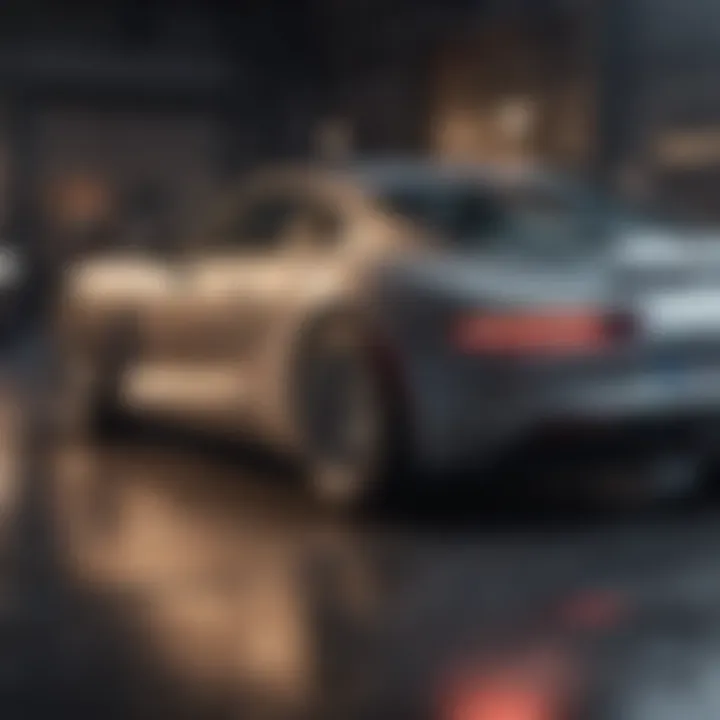
Optimizing Wall Thickness plays a pivotal role in achieving exceptional outcomes in HP MJF design. The precise calibration of wall thickness contributes significantly to the structural integrity and stability of the final product. Design engineers meticulously assess wall thickness to ensure optimal performance characteristics and product durability. Striking a balance between thickness and material utilization is key to enhancing the overall quality and viability of HP MJF components.
Support Structures Considerations
Delving into Support Structures Considerations sheds light on the intricate support systems required during the printing process. These structures provide stability and prevent deformities in intricate designs by bolstering overhanging features. The strategic placement and design of support structures are critical in enabling successful printing of complex geometries. Adhering to best practices in support structure optimization enhances print accuracy and minimizes post-processing requirements.
Part Orientation Strategies
Part Orientation Strategies are indispensable in optimizing the printing process for superior results. Proper orientation of parts within the build chamber influences print quality and minimizes the risk of defects. Engineers strategically position components to mitigate warping, improve surface finish, and optimize printing speed. Effective part orientation strategies streamline production workflows, ensuring efficient use of materials and maximizing printing success rates.
Enhancing Mechanical Properties
Material Selection Criteria
Meticulous consideration of Material Selection Criteria elevates the performance and reliability of HP MJF components. Engineers evaluate material properties such as strength, flexibility, and heat resistance to determine the most suitable option for specific applications. The selection of high-quality materials enhances structural integrity, wear resistance, and overall functionality of printed parts. By selecting materials that align with design requirements, designers optimize mechanical properties and ensure superior end-product performance.
Feature Size and Resolution
The intricacies of Feature Size and Resolution significantly impact the final quality of HP MJF components. Precision in defining feature sizes and resolutions is crucial for achieving detailed and accurate prints. Engineers meticulously tailor features to meet design specifications, ensuring dimensional accuracy and part functionality. Fine-tuning feature size and resolution parameters enhances print precision, detail clarity, and overall part consistency.
Surface Finish Recommendations
Comprehensive Surface Finish Recommendations are vital in enhancing the visual appeal and tactile quality of HP MJF components. Designers leverage finishing techniques such as tumbling, sanding, and polishing to refine surface textures and eliminate imperfections. Implementing surface finish recommendations results in aesthetically pleasing parts with improved mechanical properties and corrosion resistance. By integrating appropriate finishing processes, designers achieve exceptional surface quality and elevate the overall product aesthetics.
Ensuring Printability and Build Success
Overhangs and Bridges Optimization
Optimizing Overhangs and Bridges is essential for ensuring successful printing outcomes in HP MJF technology. Designers strategically design support structures and incorporate overhang angles to enhance print stability and minimize material wastage. By optimizing overhangs and bridges, engineers achieve superior print accuracy and structural integrity in complex geometries. Effective optimization of overhangs and bridges streamlines the printing process and reduces the need for extensive post-processing.
Escape Hole Implementation
The meticulous implementation of Escape Holes significantly contributes to the printability and quality of HP MJF components. Escape holes facilitate the removal of excess powder trapped within intricate geometries, ensuring thorough cleaning post-printing. Designers strategically integrate escape holes to expedite powder evacuation processes, enhance part functionality, and optimize print success rates. Implementing escape holes effectively improves print accessibility, reducing the risk of powder entrapment and enhancing overall build success.
Powder Removal and Cleaning Techniques
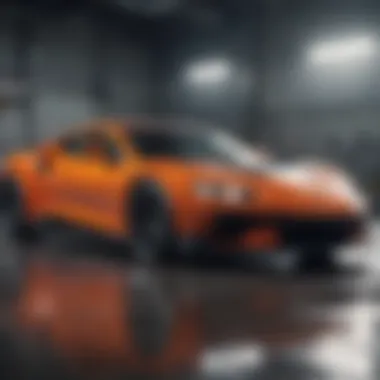

Thorough Powder Removal and Cleaning Techniques are imperative for maintaining print quality and integrity in HP MJF components. Designers employ methods such as compressed air blowing and manual brushing to remove residual powder particles post-printing. Implementing efficient cleaning techniques ensures the removal of excess powder from intricate geometries, minimizes contamination risks, and enhances part aesthetics. By adhering to rigorous powder removal and cleaning practices, engineers achieve flawless print finishes and optimize component functionality.
Implementing Efficient Post-Processing Strategies
In the realm of additive manufacturing, the importance of efficient post-processing strategies cannot be overstated. An often overlooked yet critical phase in the production process, post-processing plays a crucial role in refining the final product's appearance, durability, and functionality. By delving into the intricacies of post-processing methods, manufacturers can elevate the quality of their HP Multi Jet Fusion (MJF) printed parts to meet high standards of precision and aesthetics. From support removal to surface finishing, each step must be carefully planned and executed to ensure optimal outcomes.
Support Removal and Surface Finishing
Post-Curing Methods
Post-curing stands out as a pivotal aspect of the post-processing workflow for HP MJF printed parts. This technique involves subjecting the printed components to a controlled heat treatment process, enhancing their mechanical properties and structural integrity. The key characteristic of post-curing lies in its ability to optimize the material's curing cycle, resulting in superior part strength and dimensional stability. Manufacturers favor post-curing for its effectiveness in achieving increased material density and improved resistance to environmental factors, making it a favored choice for enhancing part performance in demanding applications.
Sandblasting and Polishing
When it comes to achieving a refined surface finish for HP MJF parts, sandblasting and polishing emerge as indispensable techniques. Sandblasting involves propelling abrasive particles against the part's surface, removing imperfections and creating a smooth texture. Polishing, on the other hand, focuses on further refining the surface through mechanical or chemical means, enhancing its visual appeal and tactile quality. The unique feature of sandblasting and polishing lies in their capacity to transform rough, post-printed surfaces into sleek, professional-grade finishes. While these techniques significantly improve the part's aesthetics, they may require meticulous attention to detail to prevent over-polishing or surface damage.
Coloring and Dyeing Techniques
Introducing color elements to HP MJF printed parts can elevate their visual impact and aid in branding or identification purposes. Coloring and dyeing techniques offer a versatile means of adding vibrant hues to the components, enhancing their aesthetic appeal and marketability. By integrating colorants into the part's surface or structure, manufacturers can customize their products to align with client preferences or industry standards. The advantages of coloring and dyeing techniques lie in their ability to provide a diverse range of color options, allowing for creativity and personalization in part design. However, careful consideration must be given to the compatibility of colorants with the base material to ensure long-term color retention and durability.
Assembly and Part Integration
Snap-Fit Design Principles
Snap-fit design principles play a fundamental role in ensuring efficient assembly processes for HP MJF printed parts. This mechanism involves designing components with interlocking features that securely join together without the need for additional fasteners or adhesives. The key characteristic of snap-fit design lies in its simplicity and ease of use, enabling rapid assembly and disassembly of parts while maintaining structural integrity. Manufacturers favor snap-fit connections for their cost-effective nature and ability to streamline the production line, making them a popular choice for various applications.
Interlocking Features
Incorporating interlocking features into HP MJF parts enhances their structural stability and robustness during assembly and use. These features consist of complementary shapes or protrusions that interlock seamlessly, forming a secure connection between components. The key characteristic of interlocking features lies in their ability to distribute mechanical loads evenly, minimizing stress concentrations and potential weak points in the structure. Manufacturers opt for interlocking designs to enhance part strength and performance, ensuring reliability in dynamic or demanding operational environments.
Multi-Part Assembly Guidelines
Navigating the complexities of multi-part assembly requires meticulous adherence to guidelines that facilitate seamless integration of components. By outlining clear instructions for aligning, connecting, and securing individual parts, manufacturers can streamline the assembly process and reduce production time. The unique feature of multi-part assembly guidelines is their comprehensive approach to coordinating complex structures, ensuring that each component fits together harmoniously to create a cohesive final product. While these guidelines promote efficiency and accuracy in assembly, proper planning and oversight are essential to avoid assembly errors or compatibility issues.
Optimizing Parameters for HP MJF Printing Process
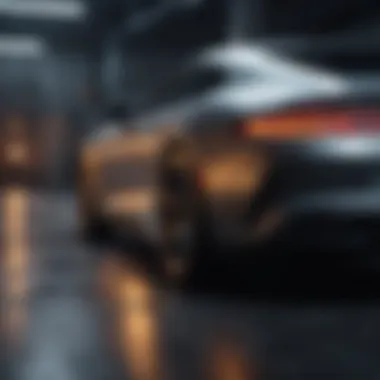
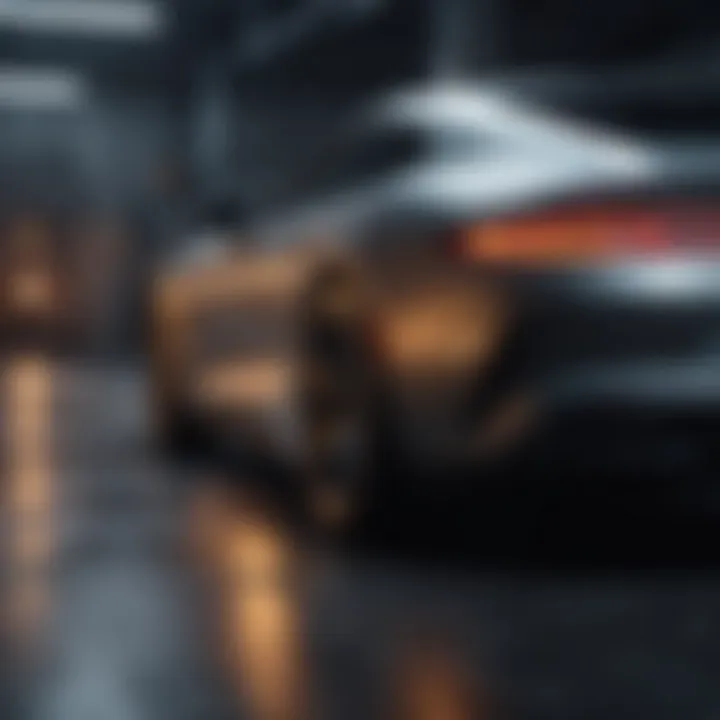
Explanation
In the domain of additive manufacturing, the optimization of parameters holds paramount importance in achieving superior results with HP Multi Jet Fusion (MJF) technology. The meticulous calibration and adjustment of print settings play a vital role in ensuring not only the quality but also the efficiency of the printing process. By focusing on specific elements such as layer thickness, resolution settings, infill patterns, density, and coolingheating rates, manufacturers can elevate the performance of their MJF printers to new heights.
Setting Optimal Print Parameters
Layer Thickness and Resolution Settings
Layer thickness and resolution settings are fundamental components of HP MJF printing that directly impact the final output. Choosing the appropriate layer thickness can significantly influence the surface finish, accuracy, and strength of the printed parts. By finely adjusting the resolution settings, manufacturers can achieve intricate details and smooth contours on their printed components. This meticulous control over layer thickness and resolution settings allows for a high level of customization and precision in manufacturing processes.
Infill Patterns and Density
The selection of infill patterns and density in HP MJF printing is crucial in determining the structural integrity and weight of the printed parts. Different infill patterns, such as honeycomb or grid structures, offer varying levels of strength and support to the printed object. By optimizing infill density, manufacturers can strike a balance between part durability and material efficiency, ensuring optimal performance while conserving resources.
Optimizing Cooling and Heating Rates
Efficiently managing cooling and heating rates during the printing process is essential for reducing thermal stresses and optimizing material properties. By controlling the temperature transitions between layers, manufacturers can mitigate warping, distortion, or cracking in the final print. Moreover, optimizing cooling and heating rates can enhance the overall mechanical properties of the printed parts, improving their durability and performance in real-world applications.
Calibration and Quality Control Measures
Dimensional Accuracy Checks
Ensuring dimensional accuracy in HP MJF printing requires rigorous quality control measures, including dimensional accuracy checks. By verifying the precise dimensions of printed parts against design specifications, manufacturers can identify and rectify any deviations or errors in the manufacturing process. Dimensional accuracy checks are essential for guaranteeing the consistency and reliability of printed components, especially in industries where tight tolerances and precise fit are critical.
Surface Inspection Techniques
Surface inspection techniques play a vital role in assessing the quality and finish of HP MJF printed parts. By employing advanced inspection methods such as visual inspection, coordinate measuring machines (CMM), or 3D scanning, manufacturers can detect surface defects, deviations, or imperfections in the printed components. These techniques enable thorough quality assessment and ensure that the final outputs meet the desired standards of aesthetics and functionality.
Performance Testing Protocols
Conducting performance testing protocols is essential for evaluating the mechanical, thermal, and overall functionality of HP MJF printed parts. By subjecting the components to various tests such as stress analysis, hardness testing, or functional assessments, manufacturers can validate the robustness and reliability of their products. Performance testing protocols provide valuable insights into the structural integrity, performance limits, and potential areas of improvement for HP MJF printed parts.
Conclusion: Driving Design Excellence with HP MJF
In the realm of additive manufacturing, Design Excellence with HP Multi Jet Fusion (MJF) holds paramount importance. As the epitome of cutting-edge technology, HP MJF offers unparalleled opportunities to push the boundaries of design innovation in various industries, particularly automotive engineering and beyond. This section encapsulates the culmination of optimizing design guidelines for HP MJF, emphasizing the pivotal role it plays in achieving superior results and ushering in a new era of manufacturing efficiency.
Delving into the essence of Design Excellence with HP MJF, we unravel a tapestry of intricate details and meticulous considerations that redefine the conventional norms of design strategies. The seamless convergence of materials, geometries, and structural integrity under the umbrella of MJF technology signifies a paradigm shift in how we conceptualize and actualize design concepts in the automotive landscape. It is not merely a process; it is an ideology that harmonizes functionality with aesthetics, durability with intricacy, elevating the very essence of design to unprecedented heights.
Through a holistic approach to optimizing HP MJF design, one transcends the realms of traditional manufacturing limitations, venturing into a realm where precision meets creativity, and efficiency aligns with artistry. Design Excellence with HP MJF mirrors a symphony of precision where every layer, every contour, and every facet harmonize to orchestrate a masterpiece of engineering prowess. It is not just about printing parts; it is about sculpting possibilities, breathing life into ideas, and etching a new chapter in the annals of automotive innovation.
As we navigate through the realm of Conclusion: Driving Design Excellence with HP MJF, we are propelled into a future where limitations are but mere illusions, and possibilities are infinite. The foundation laid by embracing HP MJF design guidelines paves the way for transformative breakthroughs, where creativity knows no bounds, and innovation knows no constraints. It is a testament to the relentless pursuit of perfection, the pursuit of excellence that fuels the heart of every automotive enthusiast, every industry professional, and every visionary at the helm of design evolution. Buckle up; the journey to design excellence with HP MJF is just beginning.