Unveiling the Impact of General Motors Factory Jobs on the Automotive Industry
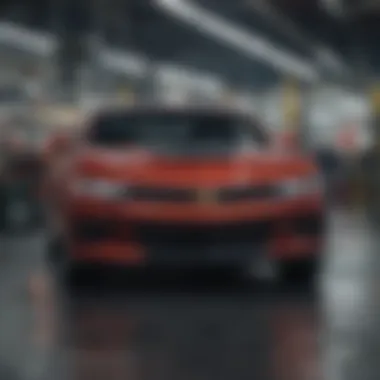
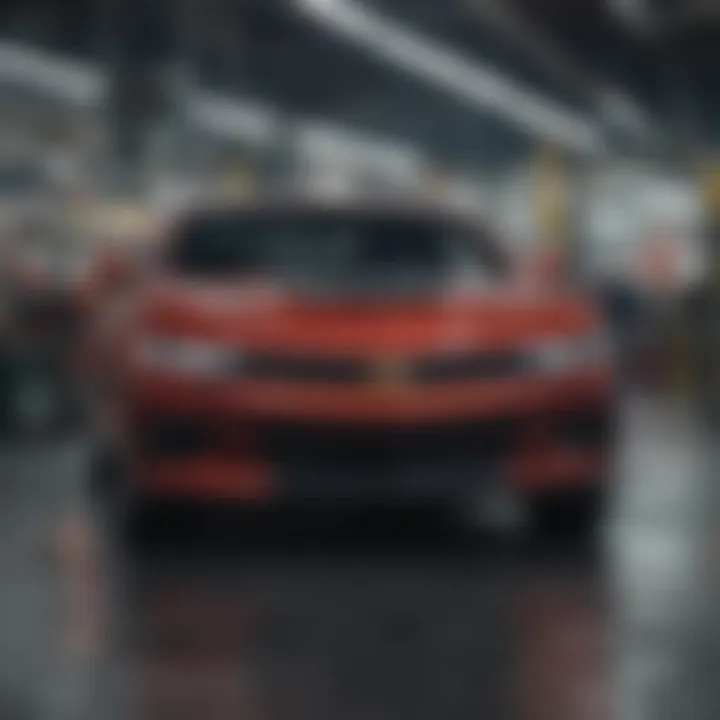
Automotive Latest News
General Motors factory jobs have long been pivotal within the automotive industry, significantly influencing the production landscape, job market dynamics, and technological progress in the sector. Stalwarts in the industry recognize the profound impact these roles have had over the years, reshaping not only the operations within General Motors but also setting precedents for automotive manufacturers worldwide. The evolution of these factory jobs continues to be a focal point in discussions surrounding production optimization, employment sustainability, and the integration of cutting-edge technologies in automotive manufacturing.
Car Reviews
Expert reviews on vehicles crafted within the General Motors factories often highlight the meticulous attention to detail, superior engineering standards, and innovative design concepts embedded in each model. Automotive enthusiasts and critics alike commend the brand for its unwavering commitment to creating not just vehicles, but driving experiences that transcend mere transportation. Comparisons with competitors reveal the unique selling points of General Motors vehicles, showcasing their performance capabilities, technological integrations, and overall value proposition in the market. User ratings also offer valuable insights into real-world experiences, shaping the narrative around General Motors' offerings and customer satisfaction.
How-To Guides
Looking beyond the showroom allure, maintenance tips for General Motors vehicles serve as indispensable resources for owners looking to prolong the longevity and performance of their investment. DIY repair guides empower enthusiasts to engage hands-on with their vehicles, fostering a sense of ownership and technical understanding. Performance upgrades further cater to individuals seeking to personalize their driving experience, exploring enhancements that elevate both style and function. These guides not only facilitate self-reliant maintenance but also foster a deeper connection between drivers and their General Motors vehicles.
Automotive Events Coverage
Auto shows stand as vibrant platforms where General Motors showcases its latest innovations, captivating audiences with futuristic concept cars, sustainability initiatives, and technological advancements. Car races provide a thrilling arena where General Motors' engineering prowess and speed dynamics are put to the test, stirring excitement among motorsport enthusiasts worldwide. Industry conferences offer a glimpse into the future trajectory of automotive trends, with General Motors often at the forefront of discussions surrounding sustainability, electrification, and autonomous driving solutions. Immersing in these events not only underscores the brand's visionary pursuits but also underscores its commitment to shaping the future of mobility.
Featured Articles
Beyond the glossy exteriors and revving engines lie behind-the-scenes narratives that unveil the meticulous processes and creative genius driving General Motors' renowned vehicles. Exploring future trends and innovations in the automotive realm provides enthusiasts with a sneak peek into what lies ahead, from advanced safety features to immersive driver experiences. These articles paint a comprehensive picture of General Motors' legacy, current endeavors, and future aspirations, offering readers a holistic view of the brand's enduring influence on the automotive landscape.
Introduction
The subject of General Motors Factory Jobs and their impact on the Automotive Industry holds a significant position within the discourse of industrial evolution. In the labyrinth of the automotive landscape, these factory jobs act as critical cogs that propel the entire machinery of production, innovation, and community integration. Delving into this domain unravels a tapestry woven with threads of historical significance, economic ramifications, and societal interplay that shape the essence of this industry.
Overview of General Motors
History and Evolution
General Motors embodies a storied legacy within the annals of automotive history. Its inception marked a pivotal juncture in the industrial revolution, heralding a new era defined by mass production and streamlined operations. The idiosyncratic path of General Motors' evolution resonates with strategic mergers, technological advancements, and market adaptability, sculpting its identity as an industry vanguard. The historical trajectory of General Motors epitomizes resilience, adaptiveness, and visionary leadership, pivotal tenets that continue to steer its course amidst ever-evolving market dynamics.
Global Presence
The expansive global footprint of General Motors stands as a testament to its enduring influence on international commerce and industrial dynamics. Spanning across continents, General Motors' operational spread intersects with diverse cultures, regulatory frameworks, and consumer preferences, fostering a rich tapestry of market insights and operational synergies. This global reach not only amplifies the brand's market visibility and accessibility but also underscores its role as a trendsetter in global automotive paradigms.
Key Contributions
The key contributions of General Motors resonate across multiple domains, ranging from technological innovations to community empowerment initiatives. Its pioneering work in fuel efficiency, safety standards, and design aesthetics has not only set industry benchmarks but has also catalyzed a culture of innovation within automotive circles. Moreover, the brand's conscientious engagement with local communities through employment generation, skill development programs, and sustainability practices underscores its commitment to holistic growth and societal well-being.
Importance of Factory Jobs
Economic Impact
The economic impact of General Motors' factory jobs reverberates beyond balance sheets, extending into the socioeconomic fabric of regions where its production facilities are stationed. These jobs serve as economic nuclei, fostering ancillary businesses, educational institutions, and infrastructural development, thereby stimulating multi-dimensional growth. The ripple effects of General Motors' factory jobs depict a nuanced economic narrative, underpinned by job creation, wealth distribution, and industrial symbiosis.
Innovation and Technology Integration
Factory jobs within General Motors propel the rhythm of innovation and technological integration, elevating production standards and product quality to unprecedented heights. The symbiotic relationship between human expertise and automated systems underscores a paradigm where efficiency, precision, and creativity converge to redefine industry benchmarks. General Motors' commitment to technological advancements reflects a strategic vision aimed at future-proofing its operations and fostering a culture of continuous improvement.
Workforce Development
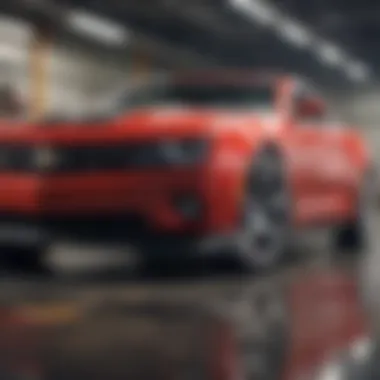
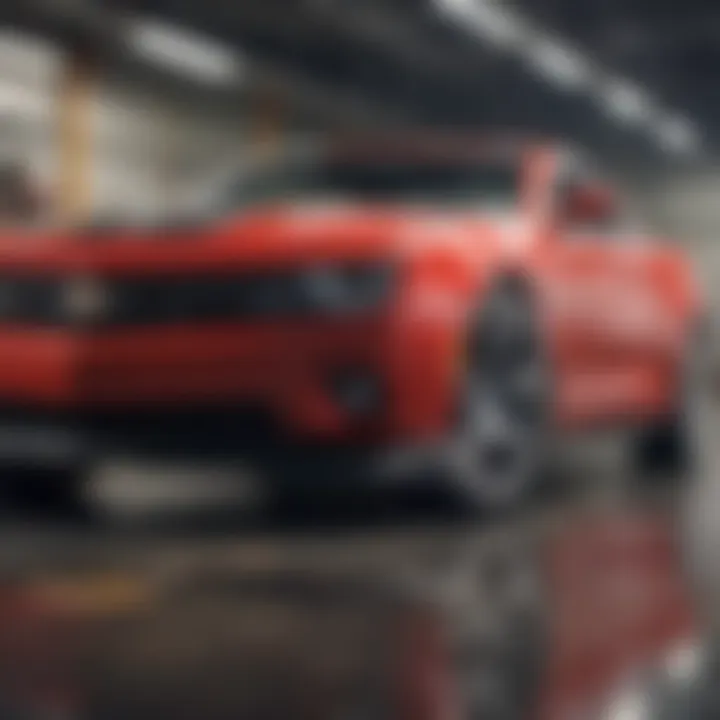
At the core of General Motors' factory operations lies a commitment to workforce development that transcends traditional skill enhancement paradigms. By nurturing a culture of continuous learning, adaptability, and cross-functional collaboration, General Motors equips its workforce with the tools to navigate industry disruptions and technological revolutions with aplomb. The emphasis on skill diversification, soft skill nurturing, and leadership grooming underscores the brand's forward-looking stance towards human capital empowerment.
Scope of the Article
Focus on Production Facilities
This article intricately examines the impact of General Motors' factory jobs on production facilities, elucidating the intricate interplay between machinery, manpower, and managerial strategies. By dissecting the nuances of production optimization, lean manufacturing principles, and quality control protocols, this section offers a panoramic view of how General Motors' production facilities epitomize efficiency, agility, and sustainability.
Impact on Local Communities
Beyond the confines of factory walls, General Motors' factory jobs resonate deeply within local communities, shaping social dynamics, economic landscapes, and environmental stewardship. The ripple effects of these jobs cascade into community upliftment programs, educational sponsorships, and environmental sustainability drives, forging a symbiotic relationship between industry progress and societal well-being.
Evolution of Factory Jobs
The evolution of factory jobs in the automotive industry is a critical aspect examined in this article. These jobs have undergone a significant transformation over the years, adapting to changing technologies and market demands. Understanding the evolution of factory jobs provides insights into how production processes have evolved and the impact on various stakeholders. This section delves deep into the historical progression, shifting from manual labor-intensive practices to more automated and innovative approaches. Highlighting the evolution of factory jobs emphasizes the importance of adapting to technological advancements to stay competitive in the automotive sector. Constant evolution is key to meeting market demands and achieving efficiency and quality standards.
Traditional Manufacturing Practices
Assembly Line Techniques
Assembly line techniques have been a cornerstone of traditional manufacturing practices. The systematic arrangement of tasks along a production line has led to significant productivity gains and cost efficiencies. One key characteristic of assembly line techniques is the division of labor, where each worker focuses on a specific task, enhancing specialization and speed. This method is a popular choice for this article due to its historical significance in revolutionizing mass production. The unique feature of assembly line techniques lies in its ability to streamline processes, reduce production time, and increase output. While advantageous in optimizing production, drawbacks include potential monotony for workers and limited flexibility in product customization.
Labor Intensity
Labor intensity refers to the level of human labor required in manufacturing processes. Historically, industries relied heavily on manual labor for production activities. The key characteristic of labor intensity is its direct correlation to production costs and output levels. It has been a beneficial choice for this article to highlight the shift towards automation and technology to reduce labor-intensive tasks. The unique feature of labor intensity is its impact on workforce dynamics and skill requirements. While manual labor was once essential for production, advancements in automation have led to increased efficiency but also challenges in reskilling the workforce. Balancing the advantages of reliable human labor with the efficiency of automation is a crucial consideration in the evolution of factory jobs.
Transition to Automation
Robotic Automation
Robotic automation plays a pivotal role in the transition of factory jobs towards modernization. The integration of robotics in manufacturing processes has enabled precision, speed, and scalability. A key characteristic of robotic automation is its ability to perform repetitive tasks with high accuracy and efficiency. This choice is beneficial for this article as it underscores the technological advancements reshaping production methodologies. The unique feature of robotic automation is its adaptability to changing production needs and ability to work in hazardous environments. While advantageous in enhancing productivity, challenges include initial setup costs and the need for maintenance expertise.
Industry Influence
The influence of Industry 4.0 in factory job evolution represents a paradigm shift towards interconnected and intelligent manufacturing systems. Industry 4.0 emphasizes the use of data, automation, and artificial intelligence to create smart factories. A key characteristic of Industry 4.0 influence is the emphasis on real-time data analysis and connectivity across production processes. This choice is beneficial for this article due to its transformative impact on industry competitiveness and efficiency. The unique feature of Industry 4.0 influence lies in its predictive maintenance capabilities and adaptive production systems. Advantages include improved decision-making and reduced downtime, but challenges include data security risks and the need for upskilling the workforce.
Skill Requirements
Technical Proficiency
Technical proficiency is a fundamental requirement in the evolution of factory jobs towards automation and digitalization. Workers need to possess the skills to operate and troubleshoot advanced manufacturing equipment. The key characteristic of technical proficiency is the ability to understand complex systems and utilize digital tools for efficient production. This choice is beneficial for this article as it highlights the importance of upskilling to meet industry demands. The unique feature of technical proficiency is its role in enhancing production quality and driving innovation. While advantageous in accelerating operational processes, challenges include the need for continuous training and adapting to rapid technological changes.
Adaptability to Change
Adaptability to change is a crucial skill in navigating the evolution of factory jobs amidst technological disruptions. Workers must be flexible and open to learning new processes and technologies. The key characteristic of adaptability to change is the willingness to embrace innovation and iterate on existing practices. This choice is beneficial for this article as it underscores the dynamic nature of modern manufacturing environments. The unique feature of adaptability to change lies in its capacity to drive organizational growth and resilience in the face of industry transformations. Advantages include improved competitiveness and agility, while challenges encompass resistance to change and training complexities.
Impact on Production Landscape
Efficiency Improvements
Amid the realm of efficiency improvements, General Motors has mobilized Lean Manufacturing Principles to streamline their production processes. This strategic approach, known for its emphasis on eliminating waste and enhancing productivity, has revolutionized General Motors' operational efficiency. The Lean Manufacturing Principles prioritize continuous improvement and lean thinking, optimizing resource utilization and minimizing operational bottlenecks. Within the context of this article, the implementation of Lean Manufacturing Principles at General Motors underscores the company's commitment to operational excellence and optimization.
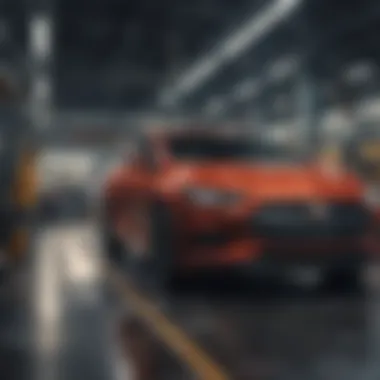
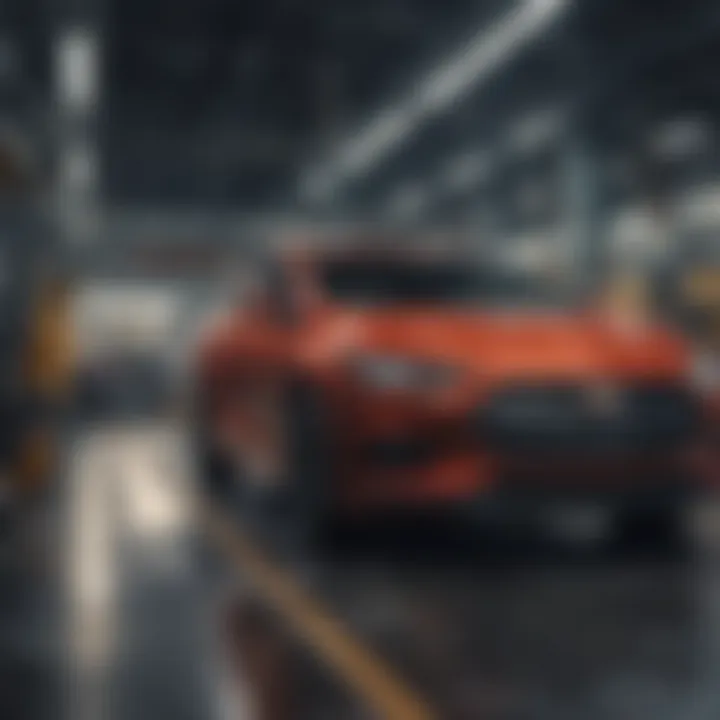
Quality Control Measures
Quality Control Measures constitute a pivotal aspect of General Motors factory operations, ensuring the delivery of high-quality vehicles to consumers. At the core of these measures lies a stringent quality assurance regime encompassing rigorous testing protocols and standardized inspection practices. By emphasizing precision and excellence in every production phase, General Motors upholds its reputation as a standard-bearer of quality in the automotive industry. The meticulous attention to detail and the adherence to stringent quality control benchmarks exemplify General Motors' unwavering commitment to producing vehicles of unmatched quality and reliability.
Product Diversification
Exploring the realm of product diversification, General Motors has responded adeptly to shifting consumer preferences by embracing Customization Trends. This strategic imperative enables General Motors to tailor their products to individual customer needs, fostering a culture of personalized vehicle design and manufacturing. By leveraging customer insights and market trends, General Motors has cultivated a diverse product portfolio that resonates with a wide range of consumers. The incorporation of Customization Trends not only enhances customer satisfaction but also propels General Motors towards market leadership and innovation.
Market Response
In the context of market response, General Motors' proactive strategies have solidified its position as a market-responsive entity. By promptly addressing consumer demands and market fluctuations, General Motors exhibits agility and foresight in navigating the dynamic automotive landscape. The company's market-responsive initiatives reflect a keen understanding of consumer preferences and market trends, enabling General Motors to position itself as a frontrunner in the competitive automotive marketplace. Through astute market analysis and responsive product development, General Motors ensures sustained relevance and competitiveness in the ever-evolving automotive industry.
Supply Chain Integration
The seamless integration of supply chain processes constitutes a cornerstone of General Motors' operational efficacy. Just-in-Time Manufacturing practices have revolutionized the company's production landscape, enabling efficient resource allocation and minimized inventory costs. By synchronizing production with demand signals, General Motors optimizes its manufacturing operations, enhancing efficiency and reducing lead times. Similarly, Logistics Optimization plays a pivotal role in enhancing General Motors' supply chain resilience and responsiveness. By optimizing transportation routes, inventory management, and distribution networks, Logistics Optimization streamlines the flow of materials and products, ensuring timely deliveries and cost-effective logistics operations.
Technological Advancements
Industry Innovations
The advent of Industry 4.0 innovations has catalyzed a paradigm shift in the automotive manufacturing domain. Within the realm of Industry 4.0, concepts like the Internet of Things (IoT) play a pivotal role. IoT facilitates seamless connectivity and data exchange between devices, enabling real-time monitoring and decision-making. Although prone to cybersecurity vulnerabilities, the IoT's ability to enhance operational efficiency and optimize resource utilization outweighs these risks.
Internet of Things (IoT)
Discussing the Internet of Things (IoT) within the context of General Motors' factory jobs underscores its essential role in streamlining production processes. The IoT's key characteristic lies in its ability to interconnect devices, enabling data-driven insights and predictive maintenance strategies. This connectivity fosters a responsive manufacturing environment, improving productivity and product quality despite potential data security challenges.
Big Data Analytics
Exploring Big Data Analytics reveals its substantial impact on operational decision-making within automotive manufacturing. The key advantage of Big Data Analytics is its capacity to process vast amounts of data swiftly, extracting valuable insights for strategic planning. While enhancing efficiency and identifying areas for improvement, integrating Big Data Analytics necessitates robust data governance to mitigate privacy and reliability concerns.
Automation Integration
Automation integration stands as a critical driver of efficiency and precision in General Motors' factory jobs. By incorporating automation technologies like cobots and predictive maintenance systems, General Motors has elevated its production standards, meeting the dynamic demands of the automotive industry.
Cobots in Manufacturin
Focusing on Cobots in Manufacturing showcases their collaborative nature alongside human workers, fostering a harmonious blend of manual and automated tasks. The key characteristic of cobots lies in their flexibility and safety features, enabling them to operate alongside human counterparts without enclosures in a shared workspace. Despite concerns about initial setup costs, the benefits of improved productivity and reduced workplace injuries underscore the value of cobots in modern manufacturing settings.
Predictive Maintenance Systems
The integration of Predictive Maintenance Systems has redefined maintenance practices within General Motors' factory operations. The key characteristic of predictive maintenance lies in its proactive approach to equipment upkeep, utilizing machine learning algorithms to anticipate maintenance needs. While enhancing production continuity and minimizing downtime, predictive maintenance systems require substantial initial data calibration and system integration to realize their full potential.
Digital Transformation
Digital transformation paves the way for enhanced operational efficiencies and immersive experiences in General Motors' manufacturing processes. Through initiatives like Smart Factory Concepts and Augmented Reality Applications, General Motors leverages digital technologies to drive innovation and improve productivity.
Smart Factory Concepts
Smart Factory Concepts embody the convergence of digital technologies with traditional manufacturing practices, facilitating streamlined production and agile decision-making. The key characteristic of smart factories lies in their real-time data analysis and automation capabilities, enabling proactive adjustments to production workflows. While enhancing response times and resource utilization, the implementation of smart factory concepts requires skilled workforce transitions and robust cybersecurity measures to protect sensitive manufacturing data.
Augmented Reality Applications
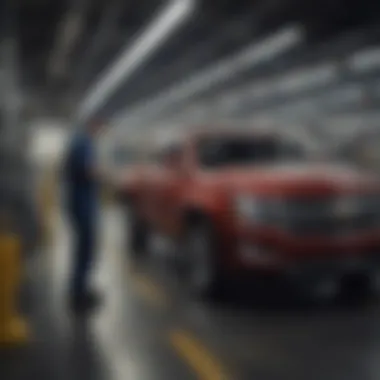
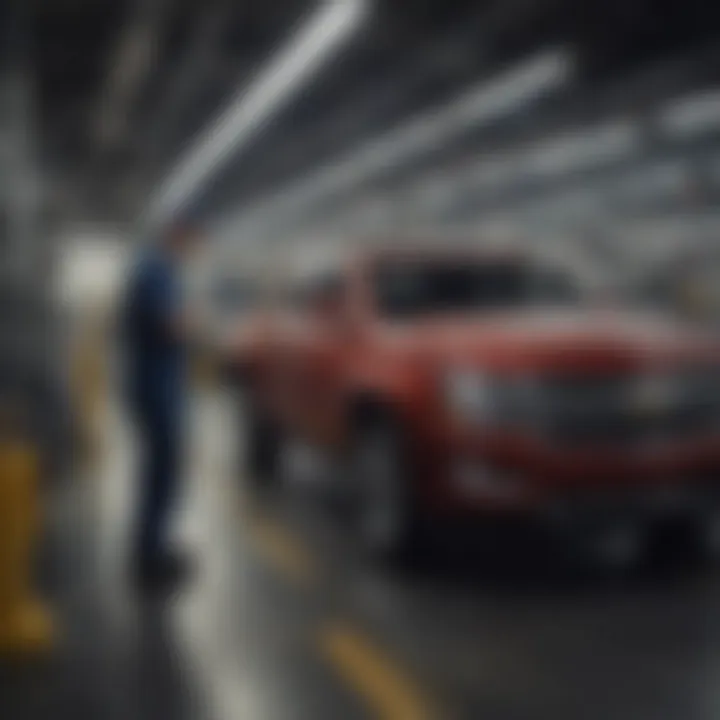
The incorporation of Augmented Reality Applications empowers General Motors' workforce with immersive training experiences and real-time insights into complex assembly processes. The key characteristic of augmented reality lies in its interactive overlays that superimpose digital information onto physical objects, enhancing worker efficiency and reducing errors in task execution. Despite the undeniable benefits of augmented reality, integrating such applications necessitates substantial initial investments in hardware and software infrastructures.
Community Impact
Factory jobs at General Motors have a significant impact not only on the automotive industry but also on the communities where these manufacturing facilities are situated. The community impact extends beyond economic aspects and delves into the social and environmental contributions made by GM factory jobs. These jobs play a pivotal role in driving local economies, supporting ancillary businesses, and fostering community development. Moreover, they provide a platform for engaging with the community through various initiatives and partnerships. The symbiotic relationship between General Motors and the local community is vital for sustainable growth and mutual benefit. This section will explore in detail the multifaceted aspects of community impact stemming from General Motors factory jobs.
Employment Opportunities
Local Job Creation
Local job creation resulting from General Motors' factory operations is a cornerstone of community impact. These job opportunities offer residents the chance to secure employment within their locality, reducing commute times and enhancing work-life balance. The creation of local jobs instills a sense of pride and ownership in the community, fostering a positive work environment and bolstering local workforce participation. The unique feature of local job creation lies in its ability to elevate economic prospects at the grassroots level, promoting financial stability and growth within the community.
Skilled Workforce Development
The focus on skilled workforce development by General Motors highlights the company's commitment to fostering talent and expertise within the community. By investing in training programs and upskilling initiatives, GM contributes to the creation of a competent workforce capable of meeting the demands of a rapidly evolving industry. The emphasis on skill development not only benefits the individuals involved but also enhances the overall competitiveness and sustainability of the local workforce. Despite some challenges, such as skill gaps and technological advancements, skilled workforce development remains pivotal in ensuring long-term growth and prosperity for both General Motors and the community.
Socio-Economic Growth
Community Investment
Community investment initiatives undertaken by General Motors have a profound effect on socio-economic growth within the local community. By channeling resources into education, healthcare, infrastructure, and social welfare programs, GM actively participates in community building and enhancement. The key characteristic of community investment is its ability to create a ripple effect, spurring further development and fostering a culture of giving back. While there may be challenges such as resource allocation and long-term sustainability, the benefits of community investment far outweigh the drawbacks, creating a more resilient and vibrant community ecosystem.
Educational Partnerships
Educational partnerships forged by General Motors with schools, colleges, and vocational institutions represent a strategic approach to promoting socio-economic growth. By collaborating with educational entities, GM enhances access to quality education, promotes STEM fields, and cultivates a skilled talent pool tailored to industry requirements. The unique feature of educational partnerships lies in their ability to bridge the gap between academia and industry, fostering innovation and knowledge exchange. Despite potential hurdles like funding constraints and logistical issues, educational partnerships play a crucial role in nurturing future generations of skilled professionals and driving socio-economic progress.
Environmental Sustainability
Green Manufacturing Practices
The adoption of green manufacturing practices by General Motors underscores the company's commitment to environmental sustainability. Through initiatives such as waste reduction, energy efficiency, and resource conservation, GM minimizes its ecological footprint and promotes responsible manufacturing. The key characteristic of green manufacturing practices lies in their ability to align business goals with environmental stewardship, benefiting both the company and the surrounding ecosystem. While challenges such as initial investment costs and regulatory compliance exist, the advantages of green practices in terms of brand reputation and long-term sustainability make them an essential component of GM's operational strategy.
Waste Reduction Strategies
Waste reduction strategies implemented by General Motors aim to optimize resource utilization and minimize environmental impact. By adopting techniques such as recycling, reuse, and waste management, GM not only reduces operational costs but also contributes to a cleaner and healthier environment. The unique feature of waste reduction strategies is their dual benefit of cost savings and environmental conservation, making them a prudent choice for sustainable manufacturing. Despite potential obstacles such as infrastructure limitations and changing regulations, waste reduction strategies remain integral to GM's commitment to environmental stewardship and corporate responsibility.
Conclusion
Summary of Key Points
Impact of General Motors Factory Jobs:
Embarking on an exploration of the impact of General Motors factory jobs reveals a tapestry woven intricately with innovation, efficiency, and economic significance. These roles serve as the backbone of the automotive industry, providing a sturdy foundation for production processes while propelling technological advancements. The distinctive characteristic of General Motors factory jobs lies in their ability to blend tradition with progress seamlessly, creating a competitive edge in the market. The advantages of these jobs lie in their adaptability to evolving industry trends, ensuring a continual relevance that drives the sector forward.
Future Trends:
Delving into future trends unveils a landscape defined by digitization, sustainability, and globalization. The reliance on advanced technologies, sustainability measures, and market expansion underscores the trajectory of the automotive industry. Future trends depict a scenario where environmental consciousness, consumer preferences, and regulatory frameworks intertwine to sculpt a dynamic outlook for the sector. Embracing these trends positions General Motors at the forefront of change, fostering resilience and foresight in a rapidly evolving market.
Final Thoughts
Continuous Evolution in Manufacturing:
Examining the concept of continuous evolution in manufacturing sheds light on the perpetual drive for improvement and progress within the industry. This aspect underscores the relentless pursuit of enhanced processes, products, and practices to stay abreast of competitors and meet consumer demands. The key characteristic of this evolution lies in its ability to fuel innovation, foster collaboration, and promote sustainable growth. Advancing manufacturing methods through continuous evolution presents opportunities for General Motors to enhance its competitive edge and solidify its market presence.
Role of Human Capital:
The role of human capital emerges as a pivotal factor in the success and sustainability of General Motors factory operations. Human expertise, creativity, and adaptability form the cornerstone of effective production processes, highlighting the irreplaceable value of skilled workforce. This characteristic sets human capital apart as a dynamic force that drives innovation, efficiency, and quality within the manufacturing ecosystem. Leveraging the potential of human capital equips General Motors with a strategic advantage, ensuring longevity and prosperity amidst ever-evolving industry landscapes.