Unveiling the Intricacies of Automotive Raw Materials: A Comprehensive Exploration
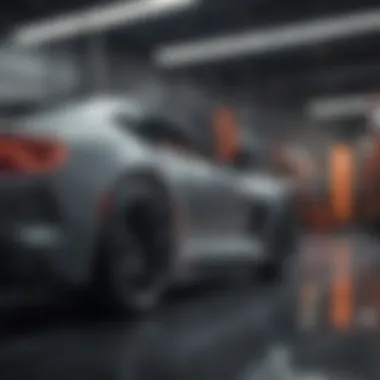
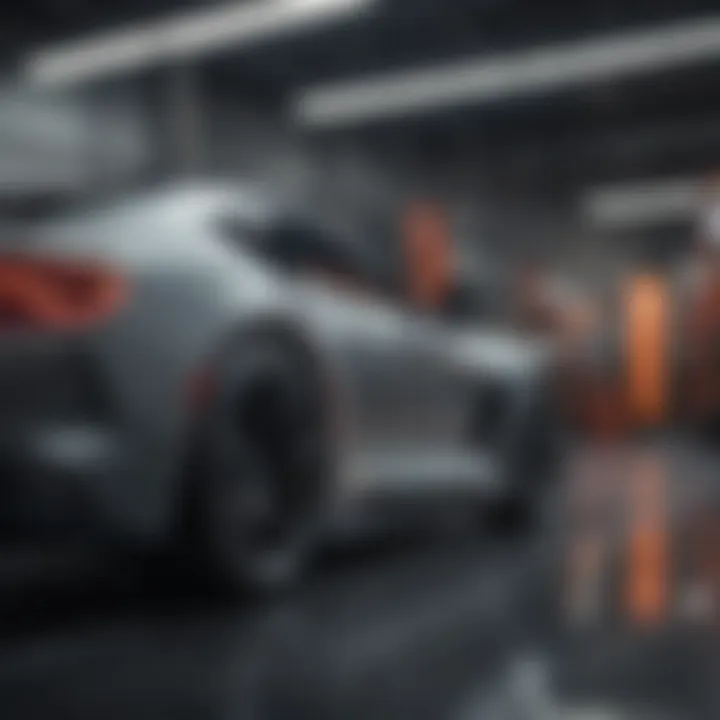
Automotive Latest News
In the fast-paced world of automotive manufacturing, staying up-to-date with the latest developments is crucial. New car launches generate immense buzz, with industry experts dissecting every detail of cutting-edge vehicles entering the market. Industry updates provide valuable insights into shifts in technology, regulations, and consumer preferences. Technological advancements like electric vehicles and autonomous driving systems are revolutionizing the industry, sparking discussions on future trends and innovations.
Car Reviews
Expert reviews offer in-depth analysis of vehicle performance, design, and features, providing readers with a comprehensive understanding of a car's strengths and weaknesses. User ratings reflect real-world experiences, offering a glimpse into customer satisfaction and reliability. Comparisons with competitors highlight how vehicles stack up against rival models in terms of pricing, performance, and overall value.
How-To Guides
Maintenance tips help car owners optimize the lifespan and performance of their vehicles, covering essential tasks like oil changes, tire rotation, and brake maintenance. DIY repair guides empower enthusiasts to tackle minor repairs independently, saving time and money. Performance upgrades offer insights into enhancing a vehicle's speed, handling, and overall driving experience through modifications and aftermarket parts.
Automotive Events Coverage
Auto shows bring together industry professionals and enthusiasts to witness the unveiling of the latest models and technological innovations in one location. Car races showcase the speed, skill, and precision of drivers competing in various disciplines, from Formula One to rally racing. Industry conferences provide a platform for key players to discuss challenges, opportunities, and future prospects in the automotive sector.
Featured Articles
Go behind the scenes at top car manufacturers to explore the design, engineering, and production processes that bring vehicles to life. Discover future trends and innovations shaping the automotive industry, from sustainable materials and green technologies to the integration of artificial intelligence and connectivity. Gain insights into the passion, dedication, and inventiveness driving the evolution of automotive raw materials.
Introduction
In the realm of automotive engineering, a foundational aspect that often garners attention is automotive raw materials. These materials serve as the building blocks upon which the entire industry rests, playing a pivotal role in every stage of the vehicle production process. The significance of understanding automotive raw materials cannot be overstated, as they directly influence not only the design and functionality of vehicles but also their performance, durability, and safety standards.
Understanding the types of raw materials used in automotive manufacturing is crucial for making informed choices regarding material selection, ensuring that the final product meets the desired performance criteria while also considering factors such as cost-efficiency and sustainability. By examining the properties and characteristics of these materials, one can gain insights into their strengths in terms of durability, weight, flexibility, corrosion resistance, and thermal conductivity, all of which are critical for producing high-quality and safe vehicles.
Moreover, the impact of sourcing and sustainability practices on the automotive industry cannot be disregarded. It is imperative to evaluate the methods of mining and extraction, assess the effectiveness of recycling initiatives, and address the environmental implications associated with the production and disposal of automotive raw materials. By incorporating sustainable practices into the sourcing and utilization of raw materials, the automotive sector can mitigate its environmental footprint and move towards a more eco-conscious future.
Navigating through the complexities of the automotive supply chain also reveals various challenges that manufacturers face, from ensuring a steady supply of raw materials to managing inventory, logistics, and production timelines efficiently. By addressing these challenges head-on, the industry can optimize its operations, enhance transparency across the supply chain, and build resilience to external disruptions, thereby fostering a more robust and sustainable automotive ecosystem.
Understanding Automotive Raw Materials
Automotive raw materials are indispensable components in the production of vehicles, shaping their design, performance, and sustainability. This section delves deep into the significance of understanding automotive raw materials within the automotive industry. By comprehending the intricacies of raw material types, properties, and sourcing practices, stakeholders can make informed decisions that impact product quality and environmental responsibility.
Types of Raw Materials
Metals
Metals serve as fundamental raw materials in automotive manufacturing, offering exceptional strength and malleability. Their robustness and ability to withstand harsh conditions make them a popular choice in the industry. Despite their benefits, metals may pose challenges such as susceptibility to corrosion and increased weight.
Polymers
Polymers are versatile materials valued for their lightweight nature and design flexibility. Their impact resistance and ease of shaping make them ideal for various components in vehicles. However, limitations like lower strength compared to metals and potential environmental implications should be considered.
Glass
Glass plays a critical role in automotive construction due to its transparency, durability, and aesthetic appeal. Its unique properties provide visibility for drivers and add structural integrity to the vehicle. Yet, glass's weight and fragility can pose challenges in certain applications.
Fibers
Fibers, including carbon and natural variants, offer high tensile strength and lightweight properties, making them essential for reinforcing composite materials. Their durability and corrosion resistance contribute to improved vehicle performance. However, the production process and cost implications should be taken into account.
Properties and Characteristics
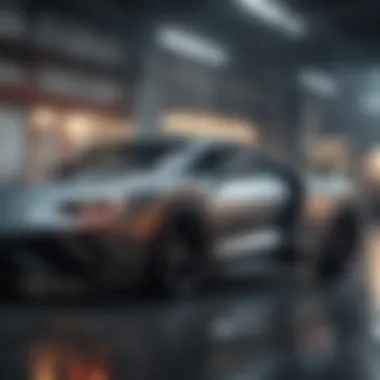
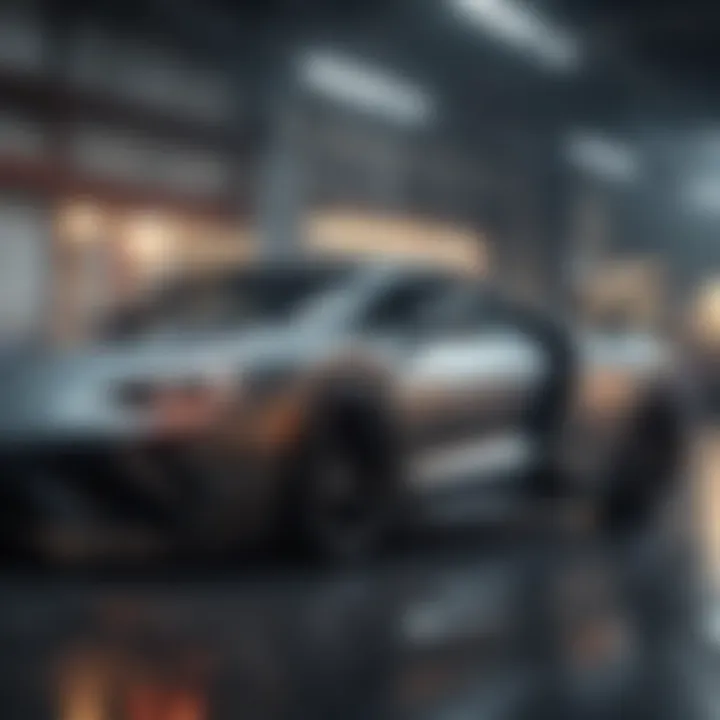
Strength and Durability
Strength and durability are vital characteristics in raw materials for ensuring the structural integrity and safety of automotive components. Materials with high strength can withstand external forces, while durability ensures long-term performance. Balancing these traits is crucial for addressing safety and longevity in vehicles.
Weight and Flexibility
The weight and flexibility of raw materials impact the overall design, fuel efficiency, and handling of vehicles. Lightweight materials reduce the vehicle's mass, enhancing fuel economy and maneuverability. However, flexibility should be optimized to maintain structural integrity and safety standards.
Corrosion Resistance
Corrosion resistance is paramount in automotive materials to prevent degradation over time. Applying protective coatings or selecting corrosion-resistant materials mitigates the impact of environmental factors, extending the lifespan of vehicle components. Maintaining corrosion resistance is essential for ensuring product quality and longevity.
Thermal Conductivity
Thermal conductivity influences the heat dissipation capabilities of materials, critical for automotive applications. Efficient thermal management ensures optimal performance and prevents overheating of crucial systems. Selecting materials with suitable thermal conductivity enhances vehicle efficiency and reliability.
Sourcing and Sustainability
Mining and Extraction
Mining and extraction processes provide the raw materials essential for automotive production. Responsible sourcing practices, including ethical mining and resource management, are crucial for mitigating environmental impacts and promoting sustainability. Balancing material availability with ecological considerations is key to fostering a more sustainable industry.
Recycling Initiatives
Recycling initiatives contribute to circular economies by reusing materials, reducing waste, and conserving resources. Implementing effective recycling programs in automotive manufacturing minimizes environmental footprints and promotes resource efficiency. Encouraging the adoption of recycling technologies advances sustainability goals in the industry.
Environmental Impact
Considering the environmental impact of sourcing raw materials is vital for promoting sustainable practices in automotive production. Evaluating factors such as carbon footprint, water usage, and waste generation guides decision-making towards eco-friendly solutions. Minimizing negative environmental consequences through conservation efforts and emissions reduction strategies is imperative for a greener automotive sector.
Supply Chain Challenges
The automotive industry faces supply chain challenges related to raw material procurement, distribution, and production coordination. Ensuring a streamlined and ethical supply chain involves addressing logistical hurdles, quality control measures, and sustainability standards. Overcoming these challenges requires collaboration among stakeholders, innovation in supply chain management, and a commitment to optimizing processes for efficiency and reliability.
Impact on Automotive Design
In this segment, we focus on the critical influence of raw materials on automotive design. A pivotal aspect in the automotive industry, design choices significantly impact a vehicle's performance, aesthetics, and overall appeal. Manufacturers carefully consider raw material properties such as strength, weight, and durability to meet safety standards and consumer expectations. The selection of materials plays a fundamental role in determining the structural integrity, functionality, and visual appeal of a vehicle. Economic factors also drive design decisions, with cost considerations influencing material choices. Innovations in materials, such as the development of high-performance and smart materials, allow for new design possibilities and enhanced functionality.
Aesthetics vs. Functionality
Aesthetics vs. functionality is a key consideration in automotive design. Balancing the visual appeal of a vehicle with its practical features is vital for creating marketable and desirable cars. Aesthetically pleasing elements, such as sleek lines and bold colors, often compete with functional aspects like safety features and aerodynamics. Striking a harmonious balance between aesthetics and functionality is essential for meeting consumer demands and staying competitive in the market. While aesthetics can attract buyers, functionality ensures that the vehicle performs optimally and meets industry standards.
Cost Considerations
Cost considerations play a significant role in material selection for automotive design. Manufacturers must balance the quality and performance of materials with production costs to maintain competitiveness in the market. Cost-effective materials that offer durability and efficiency without compromising safety or performance are highly sought after. By evaluating material costs alongside their benefits, manufacturers can optimize production processes and deliver value to customers without inflating prices.
Innovations in Materials
Innovations in materials drive advancements in automotive design. Constant research and development efforts lead to the discovery of new materials and technologies that revolutionize the industry. Lightweight composites, self-healing polymers, and energy-efficient materials are just a few examples of innovative solutions that enhance vehicle performance and sustainability. By embracing cutting-edge materials, manufacturers can create vehicles that are more efficient, durable, and environmentally friendly.
Trends in Material Usage
Exploring trends in material usage provides valuable insights into the evolution of automotive design and production processes. Manufacturers are increasingly adopting lightweight materials to improve fuel efficiency and reduce emissions. High-performance materials offer enhanced mechanical properties, leading to safer and more durable vehicles. Smart materials with adaptive features are revolutionizing vehicle functionality and user experience, paving the way for innovative technologies like self-repairing surfaces and energy-harvesting systems.
Lightweighting
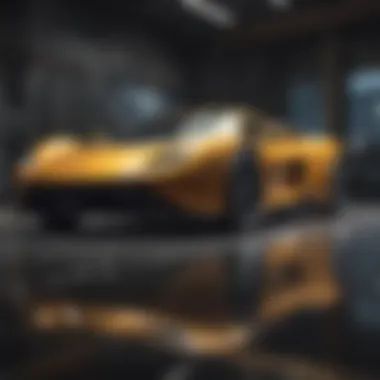
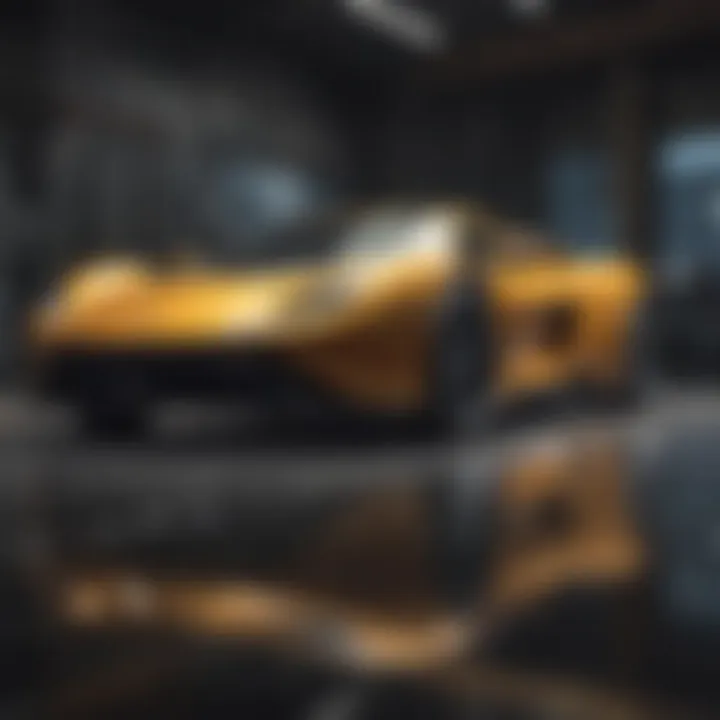
Lightweighting is a prevalent trend in the automotive industry driven by the pursuit of fuel efficiency and environmental sustainability. By utilizing lightweight materials such as aluminum, carbon fiber, and composites, manufacturers can reduce vehicle weight without compromising structural integrity. Lighter vehicles consume less fuel, emit fewer greenhouse gases, and offer improved performance, making them appealing to environmentally conscious consumers.
High-Performance Materials
The integration of high-performance materials in vehicle construction enhances durability, safety, and performance. Advanced alloys, carbon composites, and impact-resistant polymers contribute to the structural integrity of vehicles, ensuring optimal crashworthiness and occupant protection. By utilizing high-performance materials, manufacturers can meet stringent safety standards, improve driving dynamics, and deliver superior quality vehicles.
Smart Materials
Smart materials are revolutionizing the automotive industry by introducing adaptive properties and intelligent functionalities. Shape-memory alloys, self-healing polymers, and responsive textiles enable vehicles to adapt to changing conditions and user requirements. Smart materials enhance occupant comfort, facilitate advanced driver-assistance systems, and increase overall vehicle efficiency. By incorporating smart materials in vehicle design, manufacturers can create safer, more responsive, and technologically advanced automobiles.
Role in Safety Standards
The role of raw materials in ensuring safety standards cannot be understated. Crashworthiness, structural integrity, and occupant protection are paramount considerations in automotive design and manufacturing. Raw materials with high tensile strength, impact resistance, and energy absorption capabilities are essential for creating vehicles that can withstand collisions and protect occupants. By prioritizing safety standards in material selection and design, manufacturers demonstrate their commitment to producing vehicles that prioritize passenger safety and well-being.
Crashworthiness
Crashworthiness is a critical aspect of automotive safety, emphasizing a vehicle's ability to protect occupants during collisions. Raw materials with excellent energy absorption properties, such as high-strength steel, aluminum, and advanced polymers, play a vital role in dissipating impact forces and minimizing injury risks. Manufacturers conduct rigorous crash tests and simulations to evaluate the crashworthiness of vehicles and ensure compliance with regulatory standards.
Structural Integrity
Structural integrity is fundamental to the overall performance and safety of vehicles. Raw materials with high stiffness, fatigue resistance, and fracture toughness contribute to the structural integrity of vehicle components, ensuring stability and durability. By selecting materials that exhibit superior mechanical properties and resistance to deformation, manufacturers enhance the structural robustness of vehicles and reduce the likelihood of structural failure under operational conditions.
Occupant Protection
Occupant protection relies on the careful selection of raw materials that provide impact resistance, cushioning, and restraint in the event of a collision. Safety features such as airbags, seatbelts, and energy-absorbing materials are integrated into vehicle designs to safeguard occupants from harm. By incorporating materials that prioritize occupant protection and injury prevention, manufacturers enhance the safety systems of vehicles and reduce the severity of injuries sustained during accidents.
Production and Manufacturing Processes
In the realm of automotive raw materials, Production and Manufacturing Processes stand as pillars of efficiency and quality. These processes encompass the transformation of raw materials into functional components that define the performance and aesthetics of vehicles. From casting to molding to machining, each step plays a vital role in ensuring the final product meets the stringent standards of the automotive industry. By optimizing these processes, manufacturers can achieve precision, consistency, and cost-effectiveness in their production chains.
Material Transformation
Casting
Casting, a fundamental process in manufacturing, involves pouring molten material into a mold to shape it into a desired form. This method is prized for its ability to create intricate designs and complex geometries with high precision. Casting finds extensive applications in automotive production for creating engine components, transmission parts, and intricate designs in chassis structures. Its versatility and cost-efficiency make it a preferred choice for mass-producing components with intricate shapes.
Molding
Molding plays a crucial role in shaping raw materials into final products through processes like injection molding, compression molding, and blow molding. This technique is valued for its ability to produce complex shapes, enhance product strength, and ensure uniformity in dimensions. In the automotive industry, molding finds extensive use in creating interior trims, bumpers, and dashboard components. The efficiency and scalability of molding make it a popular choice for manufacturing high-volume automotive parts.
Machining
Machining involves the controlled removal of material from a workpiece to achieve the desired shape and dimensions. This precision-based process is essential for creating parts with tight tolerances and intricate features that are critical for the optimal functioning of vehicles. Machining is commonly used in crafting engine components, brake systems, and steering mechanisms. Although machining can be time-consuming for complex designs, its precision and ability to work with various materials make it indispensable in automotive manufacturing.
Quality Control Measures
Testing Procedures
Testing procedures are integral to ensuring the quality, performance, and safety of automotive components. Rigorous tests such as tensile strength testing, impact testing, and fatigue testing are conducted to evaluate the strength and durability of materials under different conditions. By subjecting components to simulations of real-world scenarios, manufacturers can identify potential weaknesses and refine their designs to meet industry standards and customer expectations.
Defect Detection
Defect detection processes involve the systematic inspection of components to identify imperfections in the material or manufacturing processes. Techniques like ultrasonic testing, X-ray inspection, and visual inspection play a vital role in detecting surface defects, internal cracks, and structural irregularities. By detecting defects early in the production stages, manufacturers can prevent costly rework, ensure product reliability, and uphold their reputation for delivering high-quality automotive components.
Compliance Standards
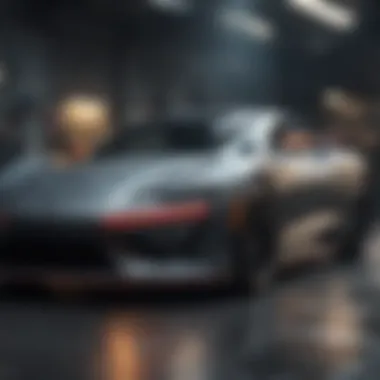
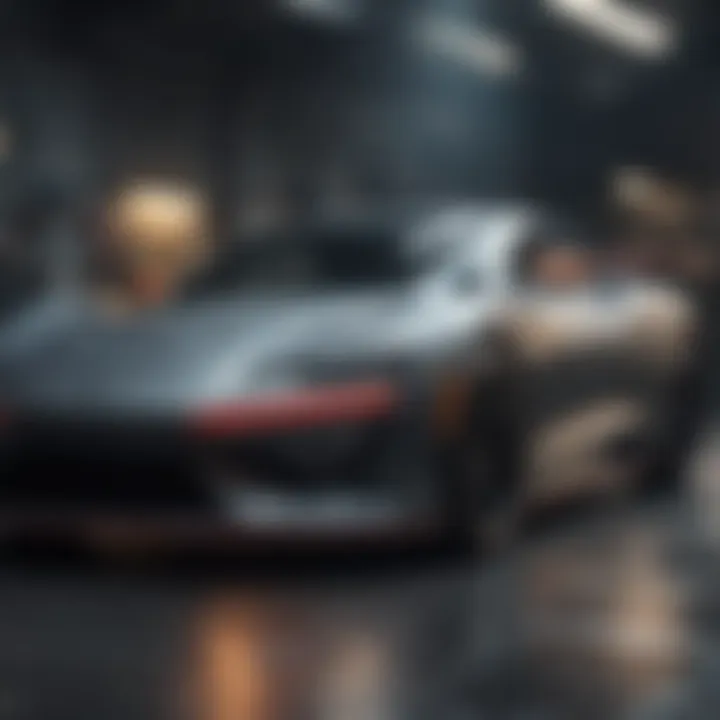
Compliance standards serve as guidelines that regulate the quality, safety, and performance of automotive products. Organizations such as ISO, ASTM, and SAE set stringent standards for materials, manufacturing processes, and product performance to ensure consistency and reliability across the industry. Adhering to these standards not only demonstrates a manufacturer's commitment to quality but also helps build trust with consumers and stakeholders, fostering a culture of reliability and excellence.
Technological Advancements
Automation
Automation has revolutionized automotive manufacturing by introducing robotics, computer numerical control (CNC) machines, and artificial intelligence into production processes. Automated systems streamline production, improve efficiency, and enhance precision in manufacturing operations. From automated assembly lines to robotic welding, automation offers manufacturers the ability to scale production, reduce lead times, and maintain consistent quality in their products.
3D Printing
3D printing, also known as additive manufacturing, enables the creation of complex geometries and customized parts with exceptional precision. This technology is increasingly adopted in the automotive industry for rapid prototyping, tooling production, and low-volume manufacturing. 3D printing reduces material wastage, allows for rapid design iterations, and facilitates on-demand production, making it a valuable asset for manufacturers seeking flexibility and innovation in their production processes.
Industry 4. Integration
Industry 4.0 integration refers to the convergence of digital technologies with physical manufacturing processes to create 'smart factories' that are interconnected, data-driven, and highly efficient. Concepts such as the Internet of Things (Io T), big data analytics, and cloud computing empower manufacturers to optimize production, monitor systems in real-time, and predict maintenance needs. By embracing Industry 4.0 principles, automotive manufacturers can achieve greater productivity, sustainability, and competitiveness in a rapidly evolving industry landscape.
Future Prospects and Innovations
In the realm of automotive raw materials, delving into future prospects and innovations is pivotal. Understanding the emerging trends and potential advancements can offer significant insights for industry enthusiasts and professionals. The continuous evolution of materials research holds the key to enhancing automotive design, production processes, and overall sustainability efforts. Envisioning the future landscape of automotive raw materials involves exploring cutting-edge technologies, novel materials, and groundbreaking methodologies.
Emerging Materials Research
Nanomaterials
Nanomaterials represent a revolutionary aspect of modern materials research within the automotive sector. Their exceptional properties, characterized by their incredibly small size and unique chemical composition, have sparked interest due to their potential to enhance material strength, durability, and performance. Nanomaterials play a crucial role in achieving lightweighting goals and boosting fuel efficiency, making them a preferred choice in automotive advancements. Despite their promising benefits, challenges like manufacturing scalability and regulatory concerns need addressing to fully leverage their advantages.
Biodegradable Polymers
Biodegradable polymers present a sustainable solution in the pursuit of eco-friendly automotive materials. Their ability to decompose naturally over time reduces environmental impact and promotes circular economy principles. The key characteristic of biodegradable polymers lies in their renewable nature and biocompatibility, making them an attractive option for manufacturers aiming for greener practices. However, limitations in material strength and performance compared to traditional polymers necessitate ongoing research and development to enhance their viability in automotive applications.
Composite Materials
Composite materials epitomize a harmonious blend of different components to achieve superior mechanical properties, making them a sought-after choice in automotive innovation. The key characteristic of composite materials is their customization potential, allowing for tailored properties such as high strength-to-weight ratio and corrosion resistance. Their versatility contributes to advancements in vehicle design, enabling manufacturers to create intricate structures while reducing overall weight. Despite their prowess, challenges in manufacturing complexity and cost-effectiveness underscore the importance of continual refinement for widespread adoption.
Environmental Sustainability
Circular Economy Models
Circular economy models foster a holistic approach to material utilization by promoting resource efficiency and waste reduction in automotive production. The distinctive feature of circular economy models lies in their emphasis on waste diversion, recycling, and reuse strategies to minimize environmental impact. By closing the production loop and extending product lifespan, these models not only reduce carbon footprint but also drive economic benefits through resource conservation. However, logistical intricacies and infrastructural requirements pose challenges that necessitate close collaboration among stakeholders for seamless implementation.
Carbon Footprint Reduction
Carbon footprint reduction initiatives play a crucial role in mitigating greenhouse gas emissions and promoting sustainable manufacturing practices within the automotive industry. The key characteristic of carbon footprint reduction efforts is their aim to lower environmental impact through streamlined processes, energy efficiency measures, and alternative fuel utilization. By adopting cleaner technologies and operational practices, manufacturers can achieve significant reductions in their carbon footprint, contributing to global climate change mitigation efforts. Despite the positive outcomes, initial investment costs and technological transitions require careful strategic planning and resource allocation.
Renewable Material Sources
Renewable material sources hold tremendous potential in reshaping the automotive industry's approach to material procurement and production. The key characteristic of renewable material sources lies in their regenerative nature, derived from sustainable biomass, agricultural by-products, or recycled materials. By minimizing reliance on finite resources and fostering a closed-loop materials system, these sources offer a pathway towards enhancing environmental sustainability and reducing carbon emissions. However, challenges related to cost competitiveness and technological adaptations demand ongoing innovation and investment to accelerate their integration into mainstream automotive supply chains.
Innovative Applications
Self-Healing Materials
Self-healing materials represent a groundbreaking innovation in automotive surfaces and components, offering the ability to autonomously repair damage and prolong lifespan. The key characteristic of self-healing materials is their capacity to heal cracks and scratches through intrinsic or external stimulus-triggered mechanisms. By enhancing durability and reducing maintenance costs, self-healing materials have the potential to revolutionize vehicle aesthetics and longevity. However, limitations in scalability and effectiveness across different material substrates warrant further research to optimize their performance in diverse automotive applications.
Flexible Electronics
Flexible electronics herald a new era in automotive technology, allowing for the seamless integration of electronic components into curved surfaces and flexible substrates. The key characteristic of flexible electronics lies in their adaptability to complex shapes without compromising functionality, enabling innovative design possibilities in vehicle interiors and exteriors. By optimizing space utilization and enhancing user experience through interactive interfaces, flexible electronics offer a futuristic approach to vehicle connectivity and convenience. Despite their transformative potential, challenges like durability under harsh environmental conditions and mass production scalability require continuous advancements in material science and manufacturing processes.
Energy Harvesting Technologies
Energy harvesting technologies present a novel avenue for powering vehicle electronics and systems through ambient energy sources, reducing dependency on traditional power outlets. The key characteristic of energy harvesting technologies is their capability to convert mechanical, thermal, or solar energy into electrical power for various automotive applications. By tapping into renewable energy sources and enhancing vehicle energy efficiency, these technologies contribute to sustainability goals and operational cost savings. However, limitations in energy conversion efficiency and integration complexity call for further research and innovation to optimize their viability for widespread adoption in the automotive sector.