Examining Automotive Plants: Structure, Function, and Impact
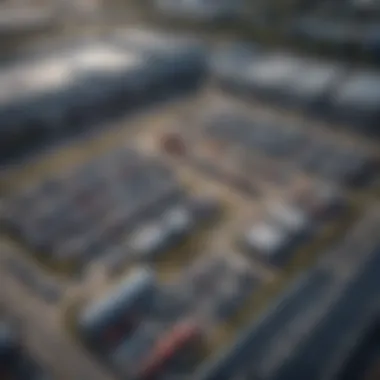
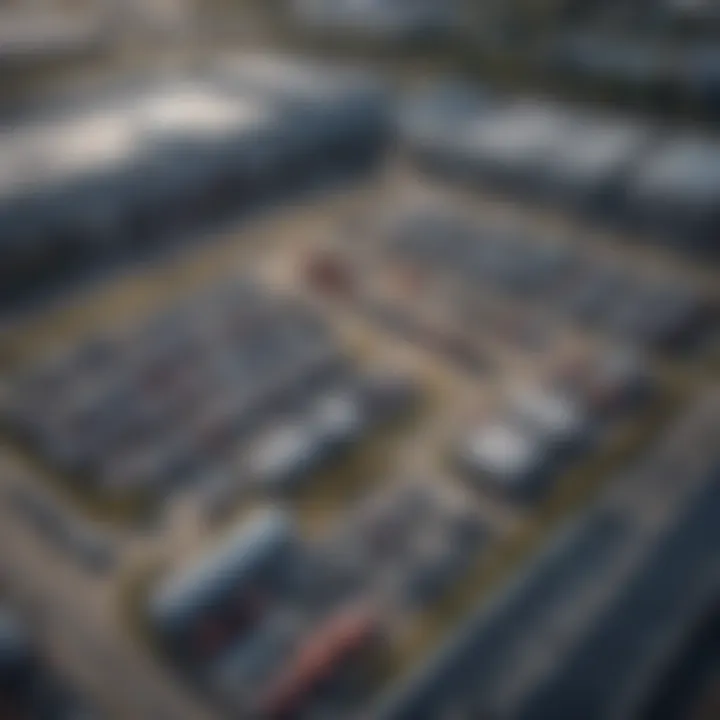
Intro
Automotive plants play a critical role in the production of vehicles, shaping not only the industry standards but also influencing economic landscapes. Understanding their structure and functions can enhance insights into how the automotive market operates. Each plant operates at the intersection of uman resource management, technology, and manufacturing efficiency.
The focus of this article will encompass how these facilities are designed, the processes they employ, the impact of technology on production, and the wider implications on automobile economies and environments. This approach ensures a thorough grasp of automotive plants’ vital roles.
Automotive Latest News
Keeping pace with the rapidly evolving automotive landscape is essential for industry professionals and enthusiasts alike. Thus, it is crucial to delve into some developments worth noting in the automobile sector:
New Car Launches
Automotive plants are often at the forefront when new models hit the market. Manufacturers like Tesla and Ford are constantly refining their production capabilities to roll out new electric and hybrid vehicles, addressing soaring consumer interest;
Industry Updates
Recent reports from the International Organization of Motor Vehicle Manufacturers highlight increasing production across Asia and North America as demand recovers. Ups and downs in sales heavily depend on the plants' readiness to adapt to shifting market dynamics.
Technological Advancements
The adoption of advanced robotics and artificial intelligence in production line operations marks a significant shift in automotive plant settings. These advancements focus on minimizing labor-intense tasks while ensuring precision. Using technology aptly reduces costs and enhances product quality, instilling greater trust in automakers from consumers.
“The future of automotive manufacturing lies in the strategic alignment of human expertise with technological prowess.”
Car Reviews
In exploring automotive plants, one must consider car reviews that cover the end product. Although this article analyzes production, the results ultimately culminate in the customer experience.
Here are elements fueling observed differences in vehicles due to varied manufacturing processes:
- Expert Reviews: Attention to detail in the assembly process often reflects in expert ratings. From reliability to innovation, insights from the reviews provide context to vitality of robust production.
- User Ratings: Feedback from everyday users enhances understanding of design operations at plants. Issues arising frequently hint at possible inconsistencies or shortcomings in production quality.
- Comparison with Competitors: Evaluation against competitors clarifies where one manufacturer may excel or falter, oftentimes linked to differences in techniques or technologies used within their automotive plants.
How-To Guides
Understanding this practical element complements the theoretical discourse on production in automotive plants. Consumers tend to value insights they can apply to modificarion, enhancing the overall experience. In this section:
- Maintenance Tips: Recommendations for owner maintenance extend vehicle longevity. Familiarity with manufacture practices helps users safeguard components built on precise standards.
- DIY Repair Guides: Learning about production technologies could empower car owners during repairs or modifications, thus fostering deeper sponsor for plants!
- Performance Upgrades: Optimizing production efforts translate to better performance adaptation through upgrading processes to ensure efficiency tailored to best output requirements.
Automotive Events Coverage
Various automotive events showcase elements in plant showcases, underscoring both research advancements and public reception. Major topics featured include:
- Auto Shows: New developments are prominently presented, giving onlookers insight into manufacturing's trajectory as facilitated by innovative plants.
- Car Races: Enthusiasts enjoy borrowing knowledge from production years, identifying champions based on constructive practices from automakers, enriching an understanding of critical production elements.
- Industry Conferences: Such events often delve into broader talks on production measures highlighting how plants innovate, adopt, and impact core operational ideologies.
Featured Articles
Deep analysis articles reveal considerable findings pertaining to automotive plants' consequential sway.
- Behind-the-Scenes at Car Manufacturers: It can unveil unseen production challenges that process improvements target, situated against competitor practices sweeping the automotive leaders' race.
- Future Trends and Innovations: Parallels from innovations point to direction various plants begin taking, proclivity toward electric and autonomous vehicles, hinting at evolving factory formats awaiting realization in facilities globally.
Through exploring automotive plants comprehensively, readers can anticipate not just understanding current conditions affecting output but dissect changing frameworks emblematic to future innovations along manufacturing lanes.
Prologue to Automotive Plants
Automotive plants are pivotal within the global automotive industry. Their structure and functions play a crucial role in the design, manufacturing, and assembly of vehicles. These facilities bring together essential technological innovations and human expertise to create complex automotive products.
Understanding the various types of automotive plants helps to appreciate the comprehensive scope of vehicle production.
Important Elements of Automotive Plants
Several core components make up the structure of automotive plants. Key manufacturing processes typically include stamping, body construction, painting, and final assembly line operations. These processes are often intertwined, leading to efficiencies and efficiencies across successive steps.
Among the notable benefits of these skilled plants are:
- Streamlined Production: Well-structured plants can significantly reduce production time.
- Quality Control: The integration of advanced technology can ensure higher quality standards.
- Flexibility: Modern plants can adjust to changes in design or production strategies quickly due to modular designs.
When assessing automotive plants, considerations such as worker safety, environmental implications, and economic footprint are paramount. A modern automotive plant must go beyond solely being a production facility; it now embodies sustainable practices and ethical labor considerations that reflect broader societal values.
The integration of the automotive plant into the local economy showcases its significance, highlighting its impact not just in production, but also in community development and job creation.
Historical Background of Automotive Manufacturing
The historical background of automotive manufacturing lays a critical foundation for understanding the industry today. Knowing the origins and key shifts in the sector enriches our perception of present challenges and innovations. Early manufacturing methods primarily focused on craftsmanship. Fast forward to today, the distinction between artisanal creation and mass production is stark. Each significant development, from assembly lines to automation, has shaped manufacturing priorities and operational structure.
Key Developments in Automotive Production

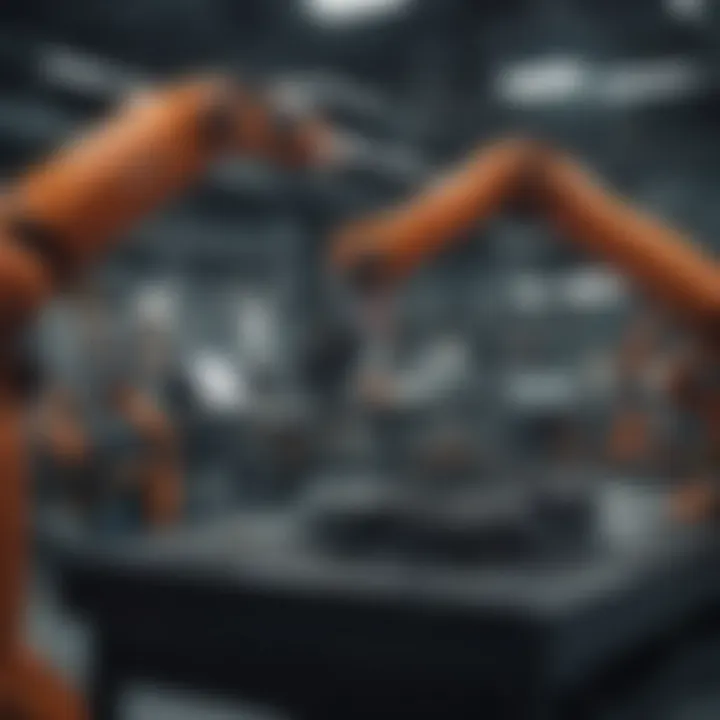
Several key developments transformed automotive production over the decades:
- Introduction of the Assembly Line: Pioneered by Henry Ford in the early 20th century, the adoption of the assembly line technique fundamentally altered production speed and efficiency. This meant vehicles could be completed faster and at lower costs.
- Advancements in Materials Science: The introduction of new materials, such as high-strength steel and composites, improved vehicle performance and safety. Materials innovation continues to influence cost-effectiveness.
- Manufacturing Automation: The use of robotics has increased precision and reduced manual labor requirements. Modern plants, like the Tesla Gigafactory, are notable for their extensive use of automation to streamline operations.
These are just a few examples, yet they highlight the ongoing evolution in production methods necessary to meet consumer demands and regulatory standards.
Evolution of Plant Design
Plant design has evolved in correspondence with the changing requirements of automotive production. Traditional layouts favored linear production while contemporary facilities focus on flexibility and efficiency.
- From Linear to Flexible Designs: Many manufacturers are moving away from rigid production lines to more flexible arrangements that allow for customization and quicker adjustments to changing model production. This has increased versatility, especially in response to shifting buyer preferences towards electric models.
- Integration of Technology: Cutting-edge technology in digital warehousing, inventory management, and real-time production tracking enhances efficiency. Smart factories utilize data analytics to optimize operations and resources.
- Sustainability Considerations: Modern plants also incorporate environmental aspects. Considerations for energy consumption, waste management, and resource recycling have gained importance, linking design with sustainability standards.
The history of automotive manufacturing illustrates a relentless pursuit of innovation and efficiency, defining how vehicles are produced now and illuminating the ongoing journey forward.
Types of Automotive Plants
The examination of automotive plants reveals their essential roles in the vehicular production ecosystem. Classifying automotive plants into various types is crucial. Each type has its specific function that contributes to the overall manufacturing process. Understanding these categories helps highlight the operational complexities and the interconnectivity within the automotive industry.
Assembly Plants
Assembly plants are integral to automotive manufacturing. They serve as the main facility where different components meet to create a complete vehicle. This final assembly process includes a host of robotic systems and human workers engaging in a synchronized workflow. Each worker on an assembly line holds a significant role, from installing engines to attaching wheels. Assembly plants can vary in scale, but large ones, such as Toyota’s factories, may produce thousands of vehicles daily.
The efficiency gained through assembly plants increases the speed of vehicle production. Companies like Ford focus on streamlined processes. This not only reduces costs but also custody production timelines. Innovations like automated assembly lines illustrate how productivity improves with technology in these plants.
Key Points of Assembly Plants:
- Volume Production: Capable of producing large quantities
- Flexibility: Adaptations to produce different vehicle models
- Efficiency: Streamlined workflows enhance productivity
Component Manufacturing Facilities
Component manufacturing is where the individual parts of vehicles are produced. These facilities specialize in distinct components, such as engines, transmissions, and electronics. Ford’s component facilities are critical to supporting their assembly plants. This interconnectedness ensures that all necessary parts are available for final assembly.
Such facilities often require specific machinery tailored to produce intricate parts. The focus here shifts towards manufacturing precision. When companies apply advanced processes, they maintain quality control while ensuring compliance with industry standards. Leading component manufacturers, like Bosch, invest heavily in technology. This results in compelling capabilities to produce state-of-the-art components efficiently and reliably.
Features of Component Manufacturing:
- Part Specialization: Focus on individual vehicle components
- Quality Control: Rigorous standards during the manufacturing phase
- Technological Investment: Advanced machinery usage enhances production capabilities
Research and Development Centers
Research and Development (R&D) centers play a pivotal role in driving innovation within the automotive industry. These centers are not merely about creating new designs but also about improving existing technologies. In these facilities, teams conduct extensive testing on materials, vehicle performance, and sustainability methods to enhance overall production methods.
A prime example is General Motors' R&D power, where cutting-edge technologies in electric vehicles are researched. This focus leads to more efficient designs and features. Working in R&D encourages collaboration across disciplines, from mechanics to software engineering, thus diversifying the knowledge exchange.
Important Aspects of R& Centers:
- Innovation Hubs: Facilitate rapid development of new ideas
- Interdisciplinary Collaboration: Teams from various fields drive improvements
- Sustainability Focus: Research includes developing greener technologies and materials
An understanding of the types of automotive plants allows stakeholders to appreciate their roles in production efficiency and technological advancements.
Key Processes in Automotive Manufacturing
The processes involved in automotive manufacturing are crucial to understanding how vehicles are produced efficiently and effectively. These processes not only ensure the quality of the final product but also influence the overall productivity of automotive plants. There are three major processes in this context: stamping and body construction, painting and finishing, and final assembly line operations. Understanding each of these processes provides valuable insight into the functionality and significance of automotive plants.
Stamping and Body Construction
Stamping and body construction are fundamental processes in automotive manufacturing. This involves shaping sheet metal into panels that will become parts of the car body. High precision in stamping is necessary to guarantee that each part fits together seamlessly. The setup often uses large hydraulic presses that can exert extensive pressure on the metal sheets. These presses are essential for creating various components including doors, hoods, and fenders.
Several key factors underpin the importance of this stage:
- Material Selection: Variability in materials used impacts durability and safety. Steel and aluminum are two primary materials for car bodies, each presenting its pros and cons.
- Cost Efficiency: Streamlining the stamping process can significantly reduce manufacturing costs. This translates into savings passed onto the consumer, boosting competitiveness.
- Quality Control: Precision in the stamping and construction phases minimizes defects which can cause failure in later usage.
Painting and Finishing
Once the body components are constructed, the next step is painting and finishing. This phase does more than provide aesthetic appeal; it also protects the vehicle. The paint needs to adhere well to the metal, resisting scratches and corrosion over time.
In this process, several critical aspects are taken into consideration:
- State-of-the-art Techniques: Modern plants employ robotic systems for painting that offer consistent coverage while minimizing waste. This significantly enhances efficiency.
- Environmental Considerations: Many manufacturers have shifted towards eco-friendly paints, reducing toxicity and emissions. This is vital for complying with increasing regulatory standards environment quality.
- Quality Assurance: Inspecting the finished paintwork is essential. Layers must align with standards and imperfections can lead to future problems. Regular audits ensure the quality remains high.
Final Assembly Line Operations
Final assembly is the concluding phase where components meet their respective systems. Each part, from the drivetrain to seating systems, comes together in a carefully orchestrated manner. Final assembly operations are complex and intricate, requiring attention to detail and coordination.
Several core elements define this stage:
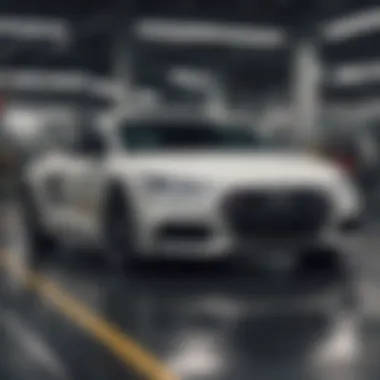
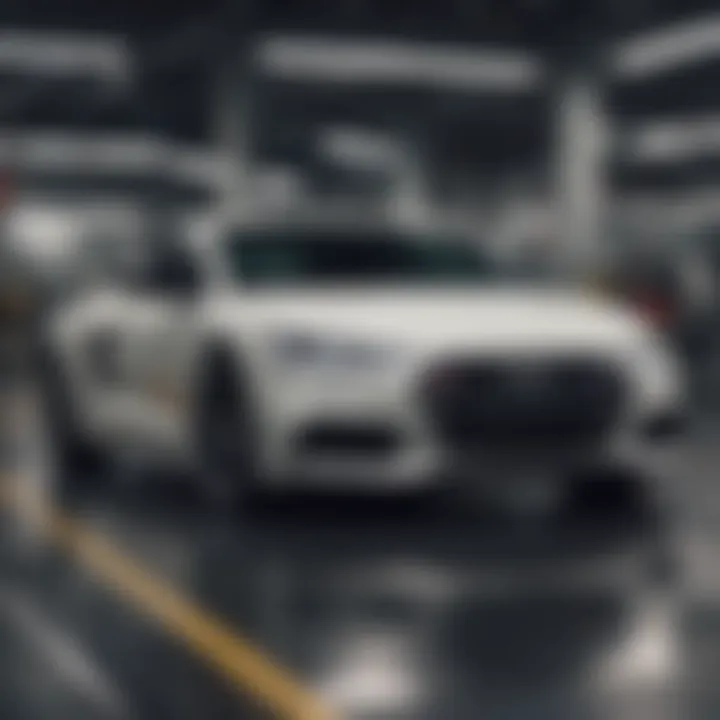
- Integrated Systems Approach: Various systems must communicate effectively. A computerized workflow ensures each part arrives at the necessary assembly point on time.
- Ergonomics in Assembly: Investing in ergonomic stations improves precision. By adjusting the workstations to the needs of workers, companies can effectively minimize injuries and maximize productivity.
- Quality Checks: Each completed vehicle undergoes rigorous testing before leaving the production line. This assures that each car is functioning correctly and ready for consumer use.
In summation, the processes of stamping and body construction, painting and finishing, along with final assembly operations define the essential framework of car manufacturing. Each phase plays a crucial role in emphasizing not only efficiency but also quality and reliability in automotive plants.
Workforce Dynamics in Automotive Plants
Understanding the workforce dynamics in automotive plants is crucial to grasp the operational efficiency and potential for innovation within the industry. The skilled workforce represents the backbone of manufacturing, influencing production quality, adherence to safety standards, and the capability to integrate advanced technologies.
Skilled Labor Requirements
The automotive industry relies heavily on skilled labor to maintain its competitive edge. Jobs within automotive plants typically require specific technical expertise, particularly in areas such as mechanical assembly, quality control, and electronics integration. With increasing complexity in vehicle design, knowledge in areas like computer programming and supply chain logistics becomes very important.
Workers must be adept at using sophisticated machinery and tools, often with minimal supervision.
Some key skills include:
- Proficiency in operating heavy machinery
- Understanding of electrical systems
- Capacity for complex problem-solving
- Strong attention to detail
Such skills promote a higher level of craftsmanship, ensuring each vehicle meets the required standards. Well-trained personnel are pivotal in fostering a culture of quality within automotive plants.
Training and Development Initiatives
To address the skilled labor need, fluctuating industry demands, and technological alterations, companies invest heavily in ongoing training and development initiatives. These programs are critical for retaining top talent. They can be structured as formal education through partnerships with local technical schools or as in-house workshops aimed at specific tasks and technologies used in the plant.
Some notable benefits of effective training include:
- Enhancing safety standards
- Increasing efficiency and productivity
- Reducing errors and waste
With emerging technologies such as automation and artificial intelligence becoming mainstream, the focus of training has shifted. Employees now need to learn to work alongside robots and manage sophisticated software interfaces. Enhancing their skill set prepares them for the evolving landscape of automotive manufacturing.
“Investing in human capital is as important as investing in machinery to ensure success in manufacturing.”
Technological Innovations in Automotive Plants
Technological innovations in automotive plants play a vital role in the advancement of the industry. They not only streamline operations but also enhance product quality and minimize costs. These innovations drive efficiency, which is essential in today's highly competitive market. Companies constantly seek new techniques to improve performance, respond to consumer needs, and adapt to regulatory requirements.
Automation and Robotics
Automation and robotics have revolutionized automotive manufacturing. These technologies increase speed and precision in production processes. Tasks such as welding, painting, and assembly have become more efficient through automation. Robots can operate tirelessly, reducing downtime and achieving consistent quality. As a result, the plants can produce a higher volume of vehicles in shorter time frames.
Moreover, this technology minimizes human error, which is crucial for maintaining safety and efficiency on the shop floor. By integrating automated systems, plants can switch between different vehicle models swiftly, adapting quickly to market demands.
Notably, this shift towards automation is not purely about replacing human workers. Instead, it allows for the upskilling of labor. Workers can focus on complex, strategic tasks rather than repetitive actions. This creates new opportunities for job roles that demand higher technical skills.
Smart Manufacturing Techniques
Smart manufacturing techniques utilize data and connectivity to enhance operations in automotive plants. This concept merges the Internet of Things (IoT) with manufacturing processes. It allows machines to communicate and share data in real time. Such connectivity enables predictive maintenance, minimizing unexpected downtimes and improving overall plant efficiency.
Additionally, these techniques foster better resource management. Real-time data allows for smarter inventory control and energy usage, aligning with sustainability goals.
Smart manufacturing also encourages a more agile production approach. By using analytics, automotive plants can anticipate consumer preferences and adjust production schedules accordingly. This level of responsiveness is essential in an era where consumer preferences often shift rapidly.
The integration of smart technologies leads to more data-driven decisions. This is integral to remaining competitive in the global automotive market.
Sustainability and Environmental Impact
Sustainability in automotive plants is crucial for the future of the industry. As environmental concerns increase, manufacturers face pressure to adopt more sustainable practices. This shift not only aligns with global efforts toward climate change mitigation but also resonates with the values of a growing segment of the conscientious consumer base. Sustainable production can lead to cost savings in the long run, providing clear economic benefits as well. A key aspect of sustainability encompasses both energy efficiency and waste management, areas that most automotive manufacturers are now prioritizing to minimize their ecological footprint.
Efforts Toward Energy Efficiency
Energy consumption is a major component of automotive manufacturing. Factories often undergo significant retrofits to reduce energy use. Innovative approaches to energy efficiency include the following:
- Upgrading Equipment: Modern machinery often uses energy more efficiently than older models. Replacing out-of-date systems can yield considerable improvements in consumption.
- Renewable Energy Sources: Many plants are investing in solar and wind energy. This transition helps reduce fossil fuel dependency and can contribute positively to a company's image.
- Lean Manufacturing Principles: These strategies aim to minimize waste, not just in terms of materials, but also energy. Streamlining processes can lead to lower overall energy use.
By implementing these strategies, automotive plants can achieve significant reductions in energy consumption. This positions the industry as a proactive player in the global push for greener practices.
Waste Management Practices
Efficient waste management is another cornerstone of sustainability in automotive plants. It's important to detail both operational practices and broader systems designed to lower waste output. Some effective strategies include:
- Recycling Materials: Efforts to recycle scrap metal, plastics, and other materials can substantially decrease the amount sent to landfills. Many plants now incorporate recycling streams into their production life cycle.
- Closed-loop Systems: Some manufacturers have developed closed-loop systems, allowing for the reuse of by-products. These systems reduce the need for raw material extraction and lower waste generation.
- Partnerships with Waste Management Organizations: Collaborating with specialized entities leads to more effective waste handling and resource recovery solutions.
As automotive plants continue to evolve, their commitment to sustainability will define their role in the global economy for years to come.
By prioritizing waste management practices within their operations, manufacturers position themselves not just as producers of vehicles, but as stewards of the environment. The link between effective systems and the reduction of negative impacts is clear, thus highlighting the importance of sustainability in today’s automotive landscape.
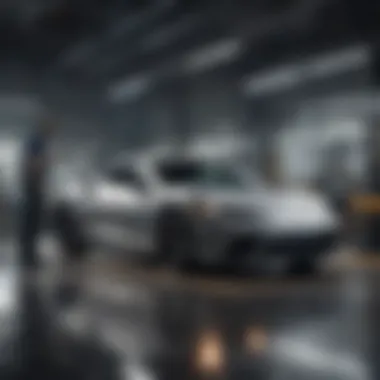
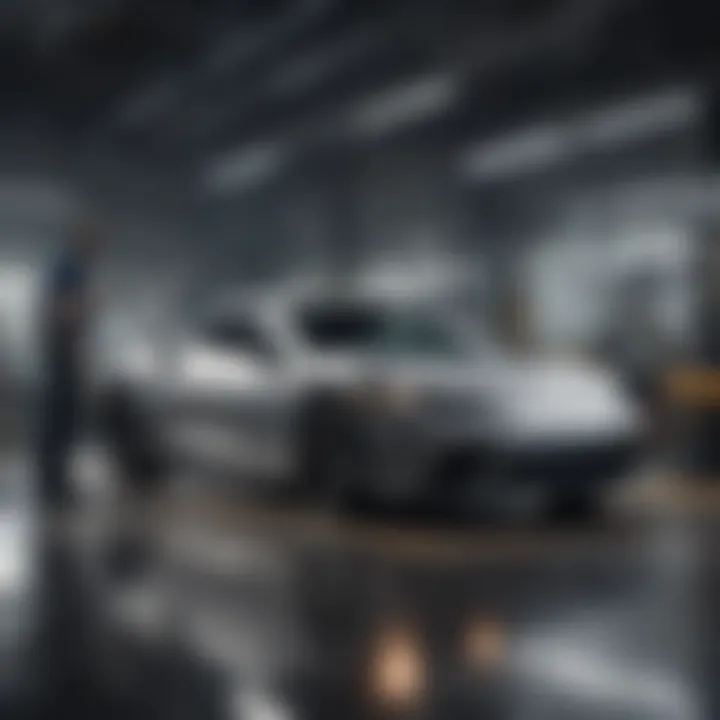
Challenges Faced by Automotive Plants
The complex landscape of automotive manufacturing involves various challenges. These challenges directly impact operational efficiency, product quality, and the overall sustainability of the industry. Addressing these issues is crucial for automotive plants to maintain competitiveness and consumer trust in a rapidly evolving market.
Supply Chain Disruptions
Supply chain disruptions have become a pressing concern for automotive plants across the world. Factors such as geopolitical tensions, natural disasters, and unforeseen pandemics can significantly impede the flow of raw materials and components to manufacturing facilities. An interruption in the supply chain can result in delays in production schedules, increased costs, and lash fallout across the entire industry.
The reliance on global sourcing of parts means that a disruption at any point in the chain can ripple through to final vehicle assembly. Just-in-time manufacturing processes, which reduce inventory costs by allowing production to adapt to changing demand, are particularly vulnerable. Automakers often find themselves struggling to manage their inventories effectively, leading to overproduction or shortages. For instance, the semiconductor shortage during the COVID-19 pandemic illustrates the vulnerability of the automotive sector to these disruptions.
Addressing supply chain vulnerabilities requires multi-layered strategies. Companies often explore diversifying their supplier base to mitigate risks and enhance resilience. Effective communication between suppliers and manufacturers ensures better transparency, helping in proactive decision-making during crisis situations.
Adapting to Regulatory Changes
Regulatory changes at local, national, and international levels present another significant challenge for automotive plants. With governments increasingly focused on environmental protection and safety standards, manufacturers must constantly update and adapt their operations in response to new legislative guidelines. Non-compliance may result in severe penalties or product recalls, both of which can harm a company's reputation and financial standing.
As consumers demand more environmentally friendly vehicles, companies face pressure to comply with stricter emissions regulations. The transition to electric vehicle production also poses regulatory challenges as factories reconfigure themselves to accommodate new technologies. Meeting efficiency claims through audits, reporting requirements on carbon footprints, and adapting to shifting standards all make balancing regulatory compliance a complex endeavor.
To manage regulatory changes effectively, automotive plants must invest in comprehensive training programs for their workforce. This not only enhances awareness of new regulations but also equips employees with the skills required to implement necessary changes. Additionally, forming partnerships with governmental agencies can facilitate smoother adaptation to compliance norms.
Overall, the challenges faced by automotive plants impact their long-term sustainability and growth. The ability to adapt and respond to supply chain disturbances as well as regulatory evolutions is crucial for surviving in the modern automotive landscape.
Future Trends in Automotive Plant Operations
The automotive industry is undergoing significant transformation. This change is especially observable in plant operations, where newer technologies and shifting consumer preferences shape the future of production. Understanding these trends is crucial for industry actors. These elements not just fortify efficiency but elevate product sterankess and adoption.
Evolution of Electric Vehicle Production
The evolution of electric vehicle production presents a notable shift for automotive plants. This shift pushes companies to rethink operational processes entirely. Key aspects influencing this evolution include:
- Technological Advancements: Continuous improvement in battery technology leads to a more efficient and sustainable production environment. Finding optimized solutions for powertrains has now become essential.
- Market Demand: The rise in consumer demand towards greener alternatives necessitates that manufacturers align their production methodologies accordingly. The public today exhibits strong awareness of climate change. Thus, preferences lean heavily toward electric vehicles.
"As we move into the next decade, it is estimated that more than 30% of the new vehicle sales globally will be battery-electric vehicles.”
- Supply Chain Innovations: The shift requires adaptative supply chains that can integrate different componentry focused on electric vehicles. Enhancing cooperation and logistics sets the tone for current manufacturing lines to handle these electrical subsystems.
As automotive plants evolve in these areas, there is an acute need for retraining workers. Skills previously linked to internal combustion engine manufacturing may become irrelevant. Upskilling the workforce becomes paramount to compete effectively.
Integration of Artificial Intelligence
The integration of artificial intelligence into automotive plant operations represents a critical advancement. Implementing AI can optimize multiple facets of productivity and decision-making. Some key points to consider include:
- Predictive Maintenance: Utilizing AI for predictive maintenance contributes to reducing downtime significantly. Systems integrated with AI can foretell equipment failures before they occur, assisting in proactive solutions.
- Quality Control: Machine learning algorithms help streamline quality assessments on an unprecedented level. Inspecting parts and assemblies in real-time ensures enhance cancellations of defects before they can enter the market.
- Manufacturing Process Automation: Automating repetitive tasks leads to increased efficiency. AI algorithms enhance operational smoothness and reduce the chances of mistake made by human laborers. Most plants engage in functions such as sorting and assembly with better supervision and security provided by AI.
By leveraging AI, automotive manufactures can also understand consumer preferences on a larger scale. Analysis of sales behavior enhances production accuracy across personal and regional markets, adapting to demands swiftly.
Integration of both electric vehicle production methodologies and artificial intelligence shapes a promising avenue for adaptation within automotive manufacturing. Keeping a keen eye on these trends positions stakeholders to make knowledgeable decisions ahead of the market shifts.
The Global Landscape of Automotive Plants
The global landscape of automotive plants is crucial for understanding the complex interplay between regional dynamics and the overarching forces of globalization that shape the car manufacturing industry. This section delves into the various operational characteristics of automotive facilities around the world. It offers insights on how regional variations, globalization, and economic conditions impact production quality, timelines, and ultimately, competitiveness in the automotive market.
Regional Variations in Plant Operations
Regional variations in automotive plant operations influence many factors from production costs to market access. Different countries have varying levels of regulatory demands, workforce availability, and infrastructure efficiencies that can shape how plants are built and how they operate. For example:
- Labor Costs: In countries such as Thailand, lower labor costs can make assembly operations highly profitable for car manufacturers. Conversely, higher labor expenses in countries like Germany necessitate greater automation and efficiency in processes.
- Compliance Requirements: In regions like the European Union, strict environmental regulations mandate facilities adopt advanced waste management and energy controls.
- Market Accessibility: Proximity to key markets influences plant operations, allowing manufacturers in North America to cater quickly and effectively to local consumer demands.
The decision to operate a plant in a specific country, therefore, hinges on a careful analysis of these variances. Addressing regional nuances equips the industry with a likelihood for sustained competitive advantage.
Impact of Globalization on Automotive Production
Globalization significantly alters automotive production. As technology advances and trade ties strengthen, the international component sourcing strategy has gained momentum. Globalization has several effects on the automotive industry:
- Supply Chain Expansion: Manufacturers can source parts from various countries at competitive prices, allowing plant operations to maximize materials costing constraints.
- Market Reach: A broader global presence gives automotive manufacturers enhanced access to emerging markets in South America, Asia, and Africa.
“Globalization has shifted production and manufacturing focus, leading to more complex supply chains while giving companies opportunities around the world.”
- Innovation through Collaboration: Collaborative partnerships for parts manufacture and R&D are more common, which fosters innovation and speeds time-to-market for new vehicle models.
The global landscape also offers challenges. Geographic dispersion of supply chains can enhance vulnerability to disruptions as seen during recent events impacting logistics worldwide. As such, a meticulous approach is required to balance risks with potential operational efficiencies that globalization provides.
End
In this article, the examination of automotive plants provides vital insights into their significant role within the broader automotive industry. Understanding the various structures and functions of these facilities allows for a clearer perspective on their impact on production efficiency, workforce dynamics, and technological innovation.
Importance of Conclusion
The conclusion of this article reinforces several key themes. It establishes that automotive plants are not merely production hubs; they are complex ecosystems that adapt to market trends and environmental considerations. Distilling the information covered through earlier sections, the conclusion highlights some critical elements that have emerged from our detailed exploration.
- Structural Significance: The design and layout of automotive plants account for both efficiency in manufacturing processes and adaptability in future technologies.
- Operational Importance: Various processes such as assembly, stamping, and final checks lay groundwork for standards in quality and speed in manufacturing.
- Impact on Workforce Dynamics: The workforce in automotive plants is comprised of skilled individuals. Continued training and development initiatives symbolize the commitment to maintaining a high standard of production skilled labor.
- Technological Integration: Growth in automation and smart manufacturing techniques illustrates a substantial shift in how production happens and how it will evolve with producing electric vehicles and integrating artificial intelligence into operations.
- Sustainability Efforts: The ongoing measures toward reducing energy consumption and improving waste management reflect European and North American regulations that contribute to a greener industry overall.
Thus, the impact of globalization and regional variations discussed throughout this article become clearer within this framework. The insights gained here exist beyond merely understanding automotive plants; they extend into understanding the fabric of modern industrial practices. The analysis of present challenges, such as navigating supply chain complexities and regulatory changes, signifies the resilience and forward-thinking ethos that permeates the automotive sector.
In summary, automotive plants play an essential role that requires ongoing evaluation and consideration. They are intrinsically linked to both historical legacies and future advancements that will shape the automobile we use now and the designs we will depend upon going forward. As these plants continue to evolve, their influence will not merely persist; it will become more critical in understanding future automotive trends and market dynamics. The comprehensive details presented here serve as a foundational aspect for those interested in and engaged with the automotive industry.